Toluene is a valuable solvent widely used in various industrial applications, including the production of paints, coatings, adhesives, and chemical reactions. However, due to its volatile nature and potential health risks, recovering toluene efficiently is crucial for both economic and environmental reasons. This article will explore the different methods of toluene recovery, their benefits, and best practices for optimizing the recovery process.
Understanding Toluene and Its Uses
Toluene, also known as methylbenzene, is an aromatic hydrocarbon with the chemical formula C₇H₈. It is a clear, water-insoluble liquid with a distinct smell and is a key ingredient in numerous industrial applications. Its ability to dissolve a wide range of organic compounds makes it an indispensable solvent in industries such as:
Paints and Coatings: Toluene is used as a solvent in the production of paints and coatings, providing the necessary consistency for application.
Adhesives: It helps in dissolving various components, ensuring a uniform and effective adhesive product.
Chemical Manufacturing: Toluene is a precursor in the synthesis of benzene, xylene, and other important chemicals.
Pharmaceuticals: It is used in the extraction and purification of active pharmaceutical ingredients (APIs).
Why Recover Toluene?
Recovering toluene from industrial processes is essential for several reasons:
Cost Savings: Reusing toluene reduces the need for purchasing new solvents, thereby cutting down operational costs.
Environmental Protection: Toluene recovery minimizes the release of volatile organic compounds (VOCs) into the atmosphere, reducing environmental pollution.
Regulatory Compliance: Many countries have strict regulations regarding the emission of VOCs. Recovering toluene ensures compliance with these regulations.
Resource Efficiency: Efficient recovery practices promote sustainable use of resources, aligning with global sustainability goals.
Methods of Toluene Recovery
There are several methods for recovering toluene, each with its own set of advantages and applications. The most common methods include:
1. Distillation
Distillation is the most widely used method for recovering toluene. It involves heating the toluene-containing mixture to its boiling point, causing the toluene to vaporize. The vapor is then condensed back into a liquid form and collected.
Advantages of Distillation:
High purity of recovered toluene.
Suitable for large-scale operations.
2. Adsorption
Adsorption involves passing the toluene-containing gas or liquid through a solid adsorbent material, such as activated carbon or zeolites. The adsorbent material captures the toluene molecules, which can later be desorbed and collected.
What is the most energy-efficient method for toluene recovery?
While each method has its own energy requirements, membrane separation is generally considered the most energy-efficient due to its lower operating temperatures and pressures. However, the choice of method depends on the specific industrial application and scale of operation.
Advantages of Adsorption:
Effective at low toluene concentrations.
Can be used in combination with other recovery methods.
3. Membrane Separation
Membrane separation utilizes selective membranes to separate toluene from a mixture. The membranes allow certain molecules to pass through while retaining others.
Advantages of Membrane Separation:
Energy-efficient process.
Can be tailored for specific applications.
4. Liquid-Liquid Extraction
In liquid-liquid extraction, toluene is separated from a mixture using a solvent that preferentially dissolves toluene. The toluene-rich solvent is then separated and processed to recover pure toluene.
Advantages of Liquid-Liquid Extraction:
Effective for complex mixtures.
Can achieve high recovery rates.
5. Solvent Recovery Machines
Solvent recovery machines are specialized equipment designed to recover solvents like toluene from waste streams. These machines typically integrate multiple recovery methods, such as distillation and condensation, to maximize efficiency.
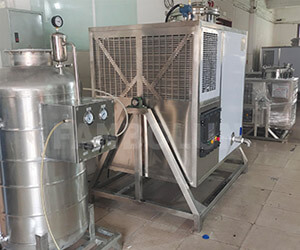
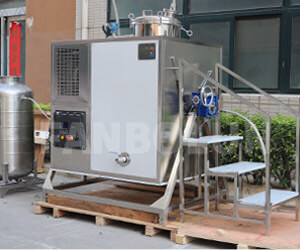
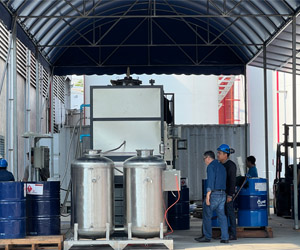
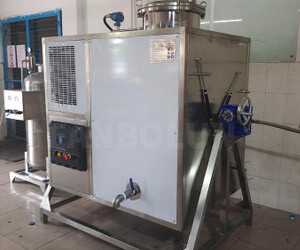
Can recovered toluene be reused in all applications?
Recovered toluene can be reused in many applications, provided it meets the required purity standards. However, for highly sensitive applications, such as pharmaceuticals, additional purification steps may be necessary to ensure the recovered toluene is free from contaminants.
Advantages of Solvent Recovery Machines:
Automated and efficient process.
High recovery rates and purity.
Reduced labor costs and minimal manual intervention.
Optimizing Toluene Recovery
To maximize the efficiency and cost-effectiveness of toluene recovery, it is essential to consider the following best practices:
1.Process Integration: Toluene is used as a solvent in the production of paints and coatings, providing the necessary consistency for application.
2.Regular Maintenance: Regular maintenance of recovery equipment ensures optimal performance and prevents downtime. This includes checking for leaks, replacing worn-out components, and calibrating instruments.
3.Monitoring and Control: Implementing advanced monitoring and control systems can help maintain optimal recovery conditions. This includes using sensors to track temperature, pressure, and toluene concentration, and adjusting parameters as needed.
4.Training and Education: Providing training and education to employees on the importance of toluene recovery and proper handling techniques can significantly improve recovery rates and safety.
How can companies ensure compliance with environmental regulations during toluene recovery?
Companies can ensure compliance by regularly monitoring emissions, maintaining accurate records of recovered toluene, and adhering to local and international environmental regulations. Implementing best practices and investing in advanced recovery technologies can also help achieve compliance.
Conclusion
Recovering toluene is not only economically beneficial but also crucial for environmental protection and regulatory compliance. By understanding the various methods of toluene recovery and implementing best practices, companies can optimize their recovery processes, reduce costs, and contribute to a more sustainable future. Whether through distillation, adsorption, membrane separation, liquid-liquid extraction, or using solvent recovery machines, the key is to select the most appropriate method for the specific application and continuously strive for improvement in recovery efficiency.