1. Paint and coating industry: Recycling and processing waste solvents generated during paint production and coating, such as gun washing water, thinner, etc.
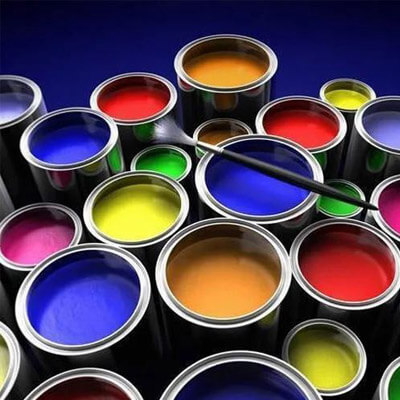
The T-90Ex is tailored for high-capacity industries needing efficient solvent recovery. With a 90L capacity and 180-minute treatment time, it's perfect for petrochemical and pharmaceutical manufacturing.
Solvent recycling equipment is a device that integrates high efficiency, environmental protection and energy saving. It uses advanced distillation and separation technology to effectively recover waste solvents generated in industrial production and convert them into reusable clean solvents, which not only reduces the company's operating costs, but also reduces pollution to the environment.
As an industry-leading environmental protection equipment, the T-90 solvent recovery machine has become an ideal choice for many companies to achieve resource recycling and reduce environmental pollution with its unique water-cooling design, bottom slag discharge method and optimized structure for treating complex waste liquids.
T-90 solvent recovery machine, as a high-efficiency water-cooled environmental protection equipment, is specially designed for the treatment of complex waste liquids, and is particularly good at dealing with the challenges of waste liquids containing oil, water and high-concentration hydrocarbons. Its unique design of the bottom slag discharge method not only ensures the stability of the equipment and the convenience of operation, but also avoids the potential safety hazards and environmental pollution caused by dumping.
During the recovery process, the T-90 solvent recovery machine showed excellent performance. Through the continuous feeding and continuous discharging mode, the efficiency of solvent recovery is effectively improved, while the downtime is reduced, meeting the demand for high-efficiency recovery equipment in industrial production. Clean liquid is efficiently collected and flows into the designated collection barrel, while dirty liquid is directly discharged through the bottom slag discharge port at the bottom of the barrel. The slag discharge method can be selected by manual operation or pneumatic slag discharge system to achieve more convenient and efficient waste slag treatment.
Efficient separation system: Advanced separation technology accurately distinguishes and recovers clean solvents, and impurities and residues are discharged smoothly through the bottom slag discharge port.
Flexible slag discharge options: The equipment provides manual slag discharge as standard, and a pneumatic slag discharge system is optional. Pneumatic slag discharge further improves the level of automation.
Continuous operation capability: Supports continuous feeding and discharging.
Wide temperature recovery range: Effectively recovers a variety of solvents with a boiling point below 210°C to meet the needs of diversified solvent recovery.
Intelligent control system: Optional pressure control system to accurately adjust the equipment operating parameters.
Environmentally friendly and energy-saving design: Water cooling method dissipates heat to reduce operating costs.
Easy to maintain: Reasonable structural design, high-quality materials, durable.
During production, customers use solvents or water to clean products, generating waste solvents. How should these waste solvents be treated, and which ones can be recycled?
1. Paint and coating industry: Recycling and processing waste solvents generated during paint production and coating, such as gun washing water, thinner, etc.
2. Automobile manufacturing and auto parts industry: Recycling and processing waste solvents generated during automobile manufacturing and maintenance, such as cleaning fluid, diluent, etc.
3. Pharmaceutical and chemical industry: Processing waste solvents in pharmaceutical and chemical production, and recovering valuable solvent components.
4. Other industrial fields: Including but not limited to electronics, hardware, textiles, printing and other industries, recycling and processing various types of industrial waste solvents.
5. Diversity of solvent types: Supporting the recycling of a variety of common solvents, such as acetone, alcohol, isopropanol, toluene, etc.
6. Customized services: Providing customized processing services to meet the special needs of different customers.
Save resources and reduce costs: The solvent recycling equipment separates and recycles the useful components in the waste solvent through the principle of distillation, effectively saving precious solvent resources. This not only reduces the demand for purchasing new solvents, but also reduces the production costs of enterprises.
Environmental protection and pollution reduction: The solvent recycling equipment reduces the emission of harmful substances by recycling and reusing solvents.
Improve production efficiency: Recycling and reusing solvents reduces the replacement and processing time of new solvents and improves production efficiency.
Efficient processing capacity: Continuous feeding and discharging ensure uninterrupted production process and improve overall work efficiency.
Precision separation technology: Adopt unique bottom slag discharge design to improve the purity of solvent recovery and reduce the complexity and cost of subsequent processing.
Intelligent control system: Real-time monitoring and adjustment of pressure to effectively avoid safety hazards such as overpressure.
Energy-saving and environmentally friendly design: Water cooling is used for heat dissipation, with higher heat dissipation efficiency and lower energy consumption.
High-quality service and support: Complete after-sales service and technical support to ensure that users can get timely and effective help during use.
Model | Feed capacity (L) | Power supply (ACV) | Power (kW) | Temperature range (℃) | Treatment time (Min.) | Recovery (%) |
T-20Ex | 20 | 380 | 2 | 5~200 | 120 | 95 |
T-60Ex | 60 | 380 | 4 | 5~200 | 150 | 95 |
T-80Ex | 80 | 380 | 5 | 5~200 | 180 | 95 |
T-90Ex | 90 | 380 | 5 | 5~200 | 180 | 95 |
T-125Ex | 125 | 380 | 6 | 5~200 | 210 | 95 |
T-250Ex | 250 | 380 | 16 | 5~200 | 240 | 95 |
T-600Ex | 600 | 380 | 32 | 5~200 | 270 | 95 |
Model | Feed capacity (L) | Power (kW) | Treatment time (Min.) |
T-20Ex | 20 | 2 | 120 |
T-60Ex | 60 | 4 | 150 |
T-80Ex | 80 | 5 | 180 |
T-90Ex | 90 | 5 | 180 |
T-125Ex | 125 | 6 | 210 |
T-250Ex | 250 | 16 | 240 |
T-600Ex | 600 | 32 | 270 |
Model: T-20EX
Feed capacity(L): 20
Power(kW): 2
Recovery(%): 95
View MoreModel: T-80EX
Feed capacity(L): 90
Power(kW): 5
Recovery(%): 95
View MoreModel: T-125EX
Feed capacity(L): 125
Power(kW): 6
Recovery(%): 95
View MoreModel: T-250EX
Feed capacity(L): 250
Power(kW): 16
Recovery(%): 95
View MoreModel: T-600EX
Feed capacity(L): 600
Power(kW): 32
Recovery(%): 95
View More