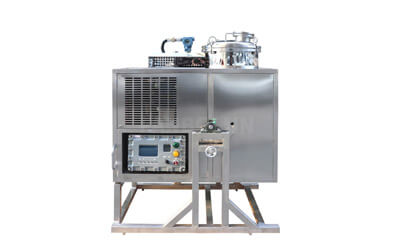
Thinner Recycler Machine (20L)
Model: T-20EX
Feed capacity(L): 20
Power(kW): 2
Recovery(%): 95
View MoreDesigned for large-scale industrial use, the T-125Ex efficiently handles 125L of solvents with a 210-minute treatment time. Ideal for coatings, inks, and cleaning solvent recovery.
Solvent recycler machine is a device that uses a specific principle (such as distillation or compressor refrigeration) to recover and regenerate waste, dirty or no longer used organic solvents.
T-125 solvent recycler machine is divided into continuous recovery type and rapid cooling type.
The T-125 continuous recycling machine adopts advanced continuous feeding and discharging technology to realize continuous recycling and treatment of solvents. This equipment usually has a larger feed capacity of 100 liters and a total barrel capacity to adapt to different scale production needs.
T-125 rapid cooling type is specially designed to solve the problem that the heat transfer oil is difficult to cool down for a long time during the recovery process, and the odor generated when opening the barrel cover spreads, affecting the working environment and the health of operators. Not only does it effectively shorten the cooling cycle by quickly reducing the temperature of the thermal oil, it also significantly reduces the release of harmful gases, providing users with a cleaner and safer working environment.
Top explosion-proof safety design: rigorous explosion-proof safety design, and successfully passed the strict testing and certification of the National Explosion-proof Supervision and Inspection Center.
Intelligent temperature control: accurately control the temperature changes during the recovery process to ensure the efficiency and stability of solvent recovery.
Triple temperature protection measures: effectively prevent overheating and ensure long-term stable operation of the equipment.
Intelligent safety system: integrated intelligent safety system, real-time monitoring of equipment operation status.
Efficient automation options: optional full-automatic continuous feeding and discharging, pressure control system, 1-inch diameter exhaust safety valve.
High-efficiency heat transfer oil circulation and intelligent rapid cooling system.
Humanized barrel design, unique horizontal barrel structure, subverts traditional design, and can easily discharge slag without dumping.
Built-in explosion-proof lamp to ensure safe lighting. High-definition window design to monitor the recovery progress in real time.
Advanced pressure control system, which can accurately control the pressure changes during the recovery process. 1-inch large-caliber stainless steel safety valve is used to effectively prevent overpressure.
Corrosion-resistant 316 stainless steel condensation system.
Continuous feeding and continuous discharging system, automated and continuous production of solvent recovery.
During production, customers use solvents or water to clean products, generating waste solvents. How should these waste solvents be treated, and which ones can be recycled?
1.Hydrocarbon solvents: such as thinner, kerosene solvent gasoline, etc. These solvents are often used for mold cleaning and product processing in the fields of precision instruments, hardware manufacturing, sports equipment manufacturing, shoe materials industry, plastic products industry and fiberglass products industry.
2.Ketone solvents: such as acetone, butanone (MEK), etc. These solvents are widely used in many industries such as automobile manufacturing and maintenance, electronic product production (such as LCD, LED cleaning), precision instruments and hardware manufacturing.
3.Aromatic hydrocarbon solvents: such as xylene, methyl ethyl ketone, etc. These solvents are often used for cleaning printing plates and machines in paint manufacturing, chemical industry and printing industry.
4.Other organic solvents: such as DMF (dimethylformamide), white oil, cleaning agents (such as thinner), isopropyl alcohol, ethanol, etc. These solvents also have important applications in their respective industrial fields, such as electronic product cleaning, paint mixing, spray equipment cleaning, etc.
Resource recycling: Solvent recycler machines use efficient recycling technology to recycle waste, polluted or no longer directly used organic solvents to obtain high-purity solvents, thereby realizing resource recycling. This helps reduce the demand for new solvents and reduce the company's raw material costs.
Compliance with regulatory requirements: With increasingly stringent environmental regulations, many countries and regions have put forward higher requirements for the discharge and treatment of industrial waste solvents. As an environmental protection equipment, solvent recycler machines can effectively reduce the discharge of waste solvents, meet the requirements of relevant regulations, and avoid legal risks and economic losses faced by companies due to illegal discharges.
Efficient recovery technology: advanced distillation or condensation technology, the recovery efficiency can reach more than 95%.
Environmental protection and safety: effectively reduce the discharge of waste solvents. Adopt explosion-proof design and safety valve.
Intelligent operation: equipped with intelligent control system to monitor various parameters in the recovery process in real time.
Durable and reliable: all made of high-quality stainless steel and other corrosion-resistant materials, with reasonable structural design, high heat transfer efficiency and low loss.
Wide applicability: suitable for the recovery and treatment of a variety of organic solvents, including but not limited to common solvents such as alcohol, isopropanol, acetone, toluene, etc.
High-quality service and support: comprehensive pre-sales consultation, in-sales guidance and after-sales service.
Model | Feed capacity (L) | Power supply (ACV) | Power (kW) | Temperature range (℃) | Treatment time (Min.) | Recovery (%) |
T-20Ex | 20 | 380 | 2 | 5~200 | 120 | 95 |
T-60Ex | 60 | 380 | 4 | 5~200 | 150 | 95 |
T-80Ex | 80 | 380 | 5 | 5~200 | 180 | 95 |
T-90Ex | 90 | 380 | 5 | 5~200 | 180 | 95 |
T-125Ex | 125 | 380 | 6 | 5~200 | 210 | 95 |
T-250Ex | 250 | 380 | 16 | 5~200 | 240 | 95 |
T-600Ex | 600 | 380 | 32 | 5~200 | 270 | 95 |
Model | Feed capacity (L) | Power (kW) | Treatment time (Min.) |
T-20Ex | 20 | 2 | 120 |
T-60Ex | 60 | 4 | 150 |
T-80Ex | 80 | 5 | 180 |
T-90Ex | 90 | 5 | 180 |
T-125Ex | 125 | 6 | 210 |
T-250Ex | 250 | 16 | 240 |
T-600Ex | 600 | 32 | 270 |
Model: T-20EX
Feed capacity(L): 20
Power(kW): 2
Recovery(%): 95
View MoreModel: T-80EX
Feed capacity(L): 90
Power(kW): 5
Recovery(%): 95
View MoreModel: T-90EX
Feed capacity(L): 90
Power(kW): 5
Recovery(%): 95
View MoreModel: T-250EX
Feed capacity(L): 250
Power(kW): 16
Recovery(%): 95
View MoreModel: T-600EX
Feed capacity(L): 600
Power(kW): 32
Recovery(%): 95
View More