Are your operations releasing harmful Volatile Organic Compounds (VOCs)? This common problem impacts air quality and health, demanding urgent attention from all of us in the industry.
Effectively controlling VOC emissions involves understanding their sources, impacts, and implementing suitable abatement technologies. For many, a solvent recycling machine offers a practical and cost-effective solution to reduce these emissions significantly.
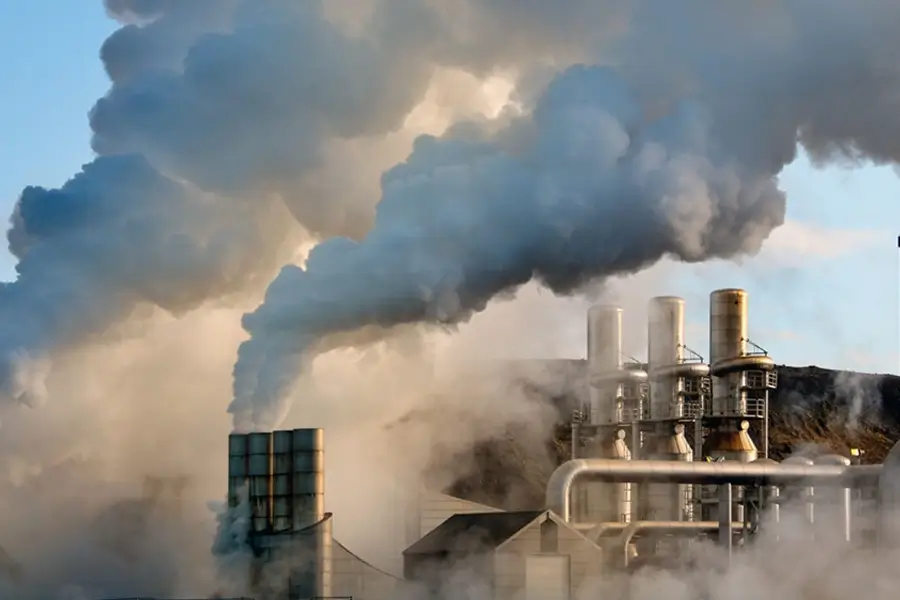
As a company with over 16 years of experience in manufacturing and exporting laboratory and industrial equipment, we've seen firsthand the growing concern over VOCs. We believe that managing these emissions is not just a regulatory hurdle, but a responsibility we all share. This article shares our insights to help you navigate this important topic. I remember when our own R&D department started focusing on cleaner solutions; it was a challenging but rewarding journey to develop equipment that helps our clients worldwide.
What Are VOCs and Why Is Controlling Them So Important?
Struggling with invisible pollutants from your processes? VOCs are these hidden culprits, often going unnoticed until regulations or health concerns bring them to light, causing widespread issues.
VOCs are carbon-containing chemicals that easily evaporate at room temperature. Controlling them is vital because they contribute to smog, can harm human health, and damage the environment. Effective management protects both people and our planet.
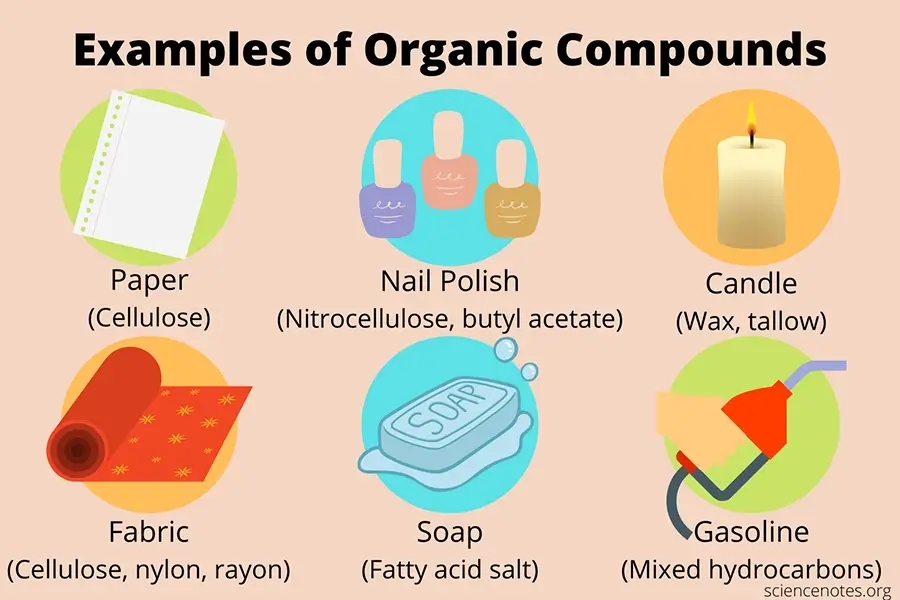
Let's break this down further. Volatile Organic Compounds, or VOCs, are a large group of chemicals. You find them in many products we use daily and in industrial processes. Think about paints, solvents, cleaning supplies, and fuels. Even some natural sources, like plants, release VOCs. However, the ones from human activities, especially industrial processes, are a major concern. I recall visiting a facility once where the smell of solvents was overwhelming; it was a stark reminder of how pervasive VOCs can be if not managed.
Common Types and Sources of VOCs:
Industrial Solvents: Acetone, xylene, toluene, and ethanol are common in manufacturing, printing, and cleaning. Many of these are essential for processes but pose emission risks.
Fuel Combustion: Gasoline and diesel combustion in vehicles and industrial machinery release VOCs like benzene.
Chemical Manufacturing: The production of plastics, resins, and synthetic rubbers can release various VOCs.
Consumer Products: Aerosols, air fresheners, and even some cosmetics contain VOCs.
Why Is Control Crucial?
The impact of uncontrolled VOC emissions is significant. Health-wise, exposure can cause anything from headaches and dizziness to long-term liver damage or cancer, depending on the specific compound and exposure level. Environmentally, VOCs react with nitrogen oxides in sunlight to form ground-level ozone, a key component of smog. This smog reduces visibility, damages crops, and harms human respiratory systems. Some VOCs are also direct greenhouse gases or contribute to their formation. Understanding what is solvent recovery can be a first step in mitigating these impacts from solvent use.
What Are the Common Methods for VOC Emission Control?
Feeling overwhelmed by the different ways to tackle VOC emissions? Choosing the right method can seem complex, with various technologies available, each with its own pros and cons.
Common methods include thermal oxidation, adsorption (like activated carbon), absorption (scrubbing), condensation, and biofiltration. The best choice depends on VOC type, concentration, flow rate, and economic factors for your specific application.
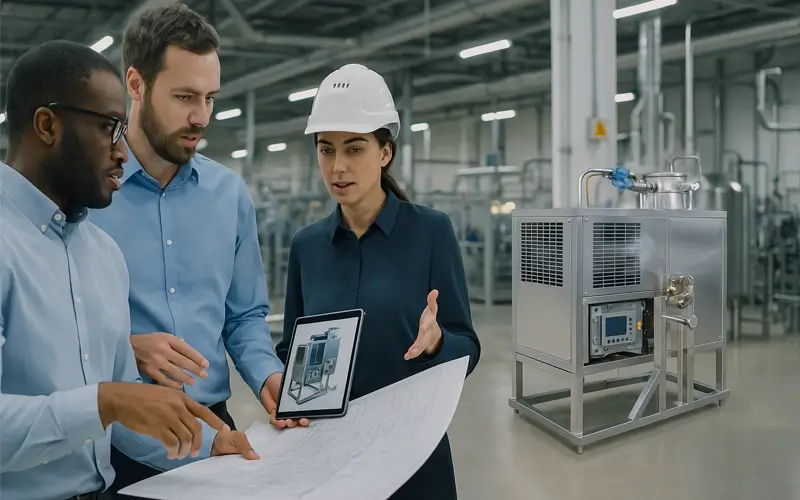
Choosing the right VOC control method is a big decision. We've helped many clients evaluate their options. Let's look at some of these methods more closely:
Control Method | Description | Pros | Cons |
---|---|---|---|
Thermal Oxidation | High-temperature combustion converts VOCs to CO2 and water. Regenerative Thermal Oxidizers (RTOs) recover heat to improve efficiency. | High destruction efficiency for many VOCs. | High energy consumption if not regenerative; can produce NOx. |
Catalytic Oxidation | Similar to thermal oxidation but uses a catalyst to allow combustion at lower temperatures. | Lower energy use than thermal; smaller footprint. | Catalyst can be poisoned or deactivated; higher initial cost. |
Adsorption | VOCs adhere to the surface of a solid adsorbent, typically activated carbon. The carbon can then be regenerated. | Effective for low VOC concentrations; can recover solvents. | Regeneration can be costly or produce waste; risk of carbon bed fires. |
Absorption (Scrubbing) | VOCs are dissolved into a scrubbing liquid. | Good for water-soluble VOCs. | Produces liquid waste that needs treatment; less effective for insoluble VOCs. |
Condensation | VOCs are cooled until they condense into a liquid, which can then be collected. Often used for solvent recovery systems. | Recovers valuable solvents; relatively simple. | Requires low temperatures for highly volatile VOCs; may need pre-cooling. |
Biofiltration | Microorganisms break down VOCs as the air stream passes through a biologically active filter bed. | Low operating cost; environmentally friendly. | Requires specific conditions for microbial activity; large footprint; slow to adapt to changing VOC loads. |
In our experience, a combination of methods or a carefully selected single method based on thorough process analysis works best. For instance, condensation is a core principle in our solvent recovery systems, making it a very practical approach for many of our clients who use solvents extensively.
How Can a Solvent Recovery System Help Reduce VOC Emissions and Save Costs?
Are you looking for a way to cut VOCs and operational expenses at the same time? Many businesses miss the opportunity to turn a waste stream into a valuable resource.
A solvent recovery system captures and purifies used solvents, drastically reducing VOC emissions from evaporation or disposal. This also cuts costs by lowering new solvent purchases and solvent waste disposal fees.
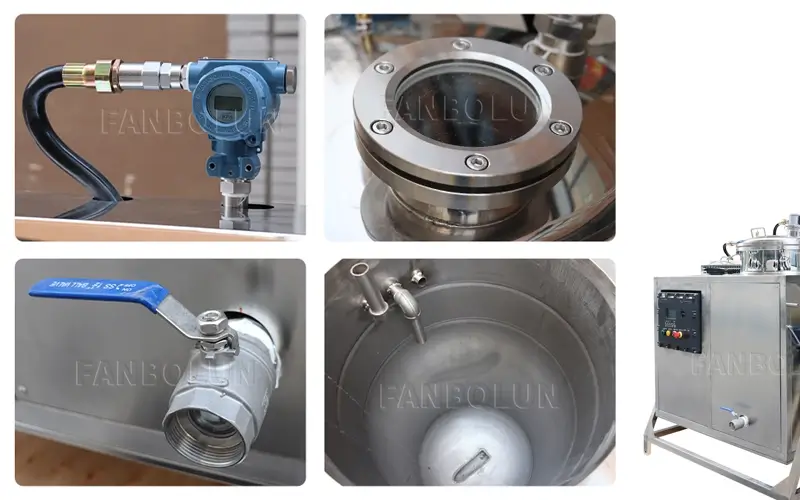
We are particularly passionate about solvent recovery because it’s a win-win: good for the environment and good for your bottom line. As a manufacturer specializing in this equipment, we've seen its transformative impact. Imagine the solvents used in your cleaning processes, extraction, or chemical reactions. Instead of letting them evaporate as VOCs or paying for their disposal, you can reclaim them.
How Our Solvent Recovery Systems Work:
Our systems typically use distillation. Here’s a simplified view:
Heating: The waste solvent mixture is heated in a controlled manner.
Vaporization: The solvent component, having a lower boiling point than contaminants, vaporizes.
Condensation: These solvent vapors are then passed through a condenser, which cools them back into a liquid state – now purified.
Collection: The pure, recovered solvent is collected for reuse, while the concentrated waste (contaminants, residues) remains in the distillation tank for proper disposal.
Benefits Beyond Emission Control:
Cost Savings: You can recover and reuse a significant percentage of your solvents (often 95% or more). This means buying much less new solvent. Think about the savings on purchasing acetone, ethanol, or methanol. For instance, proper methanol disposal can be costly, but recovering it is an asset.
Reduced Waste Disposal Costs: The volume of hazardous waste is dramatically reduced, leading to lower disposal fees and less environmental liability.
Improved Workplace Safety: Less solvent vapor in the air means a healthier environment for your employees.
Regulatory Compliance: Actively reducing VOCs helps meet increasingly strict environmental regulations.
One of our clients in the printing industry shared that after installing our solvent recovery system, they cut their solvent purchases by 70% and significantly reduced their VOC footprint. It's stories like these that drive our commitment to this technology.
What Should We Consider When Choosing a VOC Control Strategy for Our Business?
Is picking the right VOC control strategy a puzzle for your business? With many factors to weigh, it's easy to feel unsure about making the most effective and economical choice.
Consider VOC characteristics (type, concentration), air flow rate, required efficiency, capital and operating costs, available space, and regulatory requirements. A thorough site assessment and process analysis are key to selecting the optimal strategy.
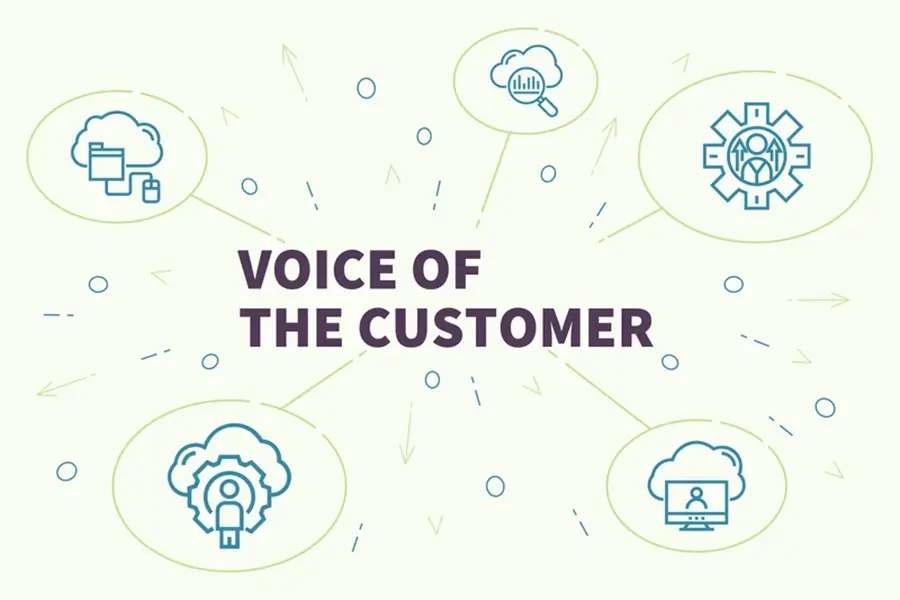
Selecting the right VOC control strategy isn't a one-size-fits-all solution. It's a careful balance of technical needs, economic realities, and long-term sustainability. Based on our 16 years of helping businesses globally, here are key factors we always discuss:
Key Considerations:
VOC Profile:
Types of VOCs: Different chemicals behave differently. Are they halogenated? Water-soluble? What are their boiling points?
Concentration: Is it a high concentration, low volume stream, or vice-versa? This heavily influences technology choice. Adsorption might be good for low concentrations, while condensation or oxidation might suit higher ones.
Flow Rate: The volume of air needing treatment per unit of time determines the size and capacity of the equipment.
Performance Requirements:
Required Destruction/Recovery Efficiency: What level of VOC reduction do regulations demand, or what are your internal environmental goals?
Variability: Does your process have consistent emissions, or do they fluctuate? The system needs to handle peak loads.
Economic Factors:
Capital Costs (CAPEX): The initial investment for the equipment and installation.
Operating Costs (OPEX): This includes energy, consumables (like carbon or catalyst), maintenance, and labor. A solvent recovery system, for example, has an upfront cost but offers significant OPEX savings by reducing solvent purchases.
Return on Investment (ROI): Especially for recovery technologies, calculate how quickly the savings will pay back the initial investment.
Site and Operational Factors:
Available Space: Some technologies, like biofilters, require a large footprint.
Utilities: What's available on site (electricity, steam, cooling water)?
Integration: How will the control system integrate with your existing processes?
Maintenance: Consider the ease of maintenance and the availability of support. We pride ourselves on our 24/7 after-sales support for this very reason.
Regulatory Landscape:
Current and Future Regulations: Ensure the chosen solution meets today's rules and has a good chance of meeting stricter future ones.
We often advise starting with a detailed audit of your VOC emissions. This data forms the foundation for making an informed decision. Sometimes, process modifications upstream can reduce VOC generation in the first place, complementing any end-of-pipe treatment. It's a holistic approach we advocate for long-term success.
Conclusion
Effectively controlling VOCs is crucial. By understanding options like solvent recovery systems, we can protect health, meet regulations, and often save money. Let's work towards cleaner air together.