Are escalating solvent costs shrinking your battery production margins? Concerned about environmental regulations? There's a smarter way to operate.
Solvent recovery in battery production is a process that reclaims and purifies solvents used in electrode manufacturing. This method significantly cuts raw material expenses, reduces waste, and helps meet environmental standards, boosting profitability and sustainability.
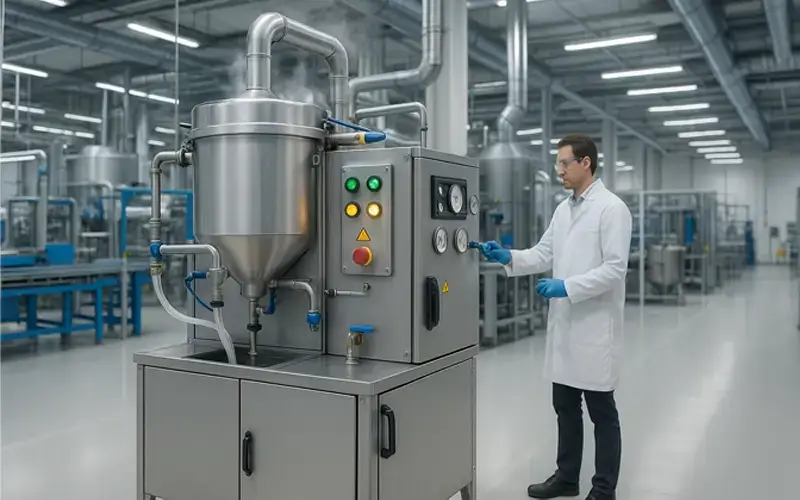
As a company with over 16 years of experience exporting advanced laboratory and production equipment, we understand the challenges in modern manufacturing. We've seen industries transform by adopting efficient technologies. The battery sector is no different. Staying competitive means optimizing every part of your process. Solvent recovery is a key optimization that many are now exploring. We want to share some of our knowledge to help you see its potential. This technology is not just an add-on; it's a fundamental shift towards smarter production.
What Exactly is Solvent Recovery and Why is it Crucial in Battery Manufacturing?
Wondering how solvent recovery fits into making batteries? Seeing those solvent purchase bills pile up? It's a game-changer for cost and eco-friendliness.
Solvent recovery systems capture, purify, and reuse valuable solvents like NMP (N-methyl-2-pyrrolidone) from the exhaust streams during electrode coating and drying. This is crucial for cutting operational costs and adhering to environmental regulations in lithium-ion battery production.
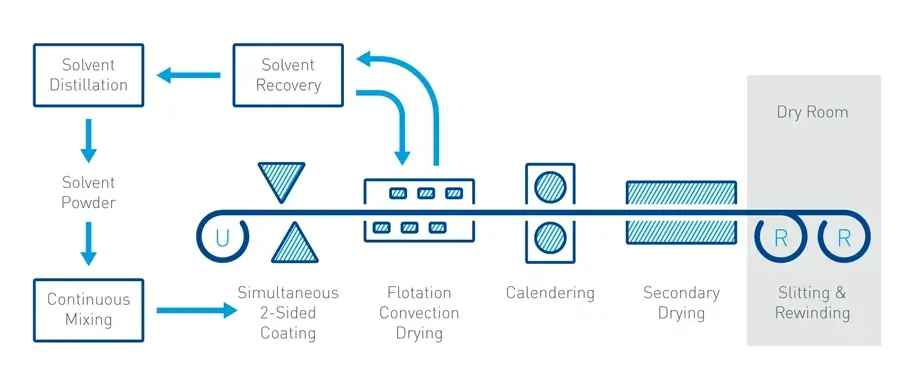
In battery manufacturing, particularly for lithium-ion cells, solvents play a vital role. The most common one is NMP. It's used to dissolve the binder material, like PVDF, which holds the active electrode materials (like lithium cobalt oxide or graphite) together and onto the current collector foils (aluminum or copper). During the electrode coating process, this solvent-based slurry is applied to the foils, and then the coated foils pass through large drying ovens. Here, the solvent evaporates, leaving a dry, porous electrode layer. Without recovery, this evaporated solvent, laden with valuable NMP, is either vented to the atmosphere (which is environmentally harmful and often illegal) or incinerated (which destroys the solvent and costs energy). Solvent recovery steps in to capture these NMP vapors. We design systems that then condense and purify this NMP, allowing it to be reused in the coating process. This closes the loop, reduces the need to purchase virgin solvent, and minimizes harmful emissions. It is a critical step for modern, large-scale battery factories.
Key Stages in Solvent-Based Electrode Manufacturing:
Mixing: Active material, conductive agent, and binder are mixed with solvent (e.g., NMP) to create a uniform slurry.
Coating: The slurry is precisely applied onto current collector foils.
Drying: Coated foils pass through ovens where the solvent evaporates. This is where solvent recovery units are integrated.
Calendering: Dried electrodes are compressed to achieve desired thickness and porosity.
How Can Implementing Solvent Recovery Slash Operational Costs for Battery Producers?
Are high solvent purchase and disposal expenses impacting your bottom line? Looking for proven ways to reduce manufacturing overhead? This is a direct path to savings.
Implementing solvent recovery directly cuts costs by drastically reducing the need to buy expensive new solvents. It also lowers waste disposal fees and potential environmental fines, leading to substantial operational savings for battery producers.
Cost Category | Without Solvent Recovery (Annual Estimate) | With Solvent Recovery (Annual Estimate) | Annual Savings with Recovery | Notes |
---|---|---|---|---|
Solvent Purchasing | ||||
New Solvent Volume (Liters) | 120,000 L | 6,000 L (assuming 95% recovery) | 114,000 L | Example: 10,000 L/month. |
Cost per Liter | $5 | $5 | - | |
Total New Solvent Cost | $600,000 | $30,000 | $570,000 | Significant reduction in new solvent purchases. |
Solvent Disposal | ||||
Waste Solvent Volume (Liters) | 120,000 L | 6,000 L | 114,000 L | Waste is significantly reduced. |
Disposal Cost per 200L Drum | $200 | $200 | - | |
Number of Drums for Disposal | 600 Drums | 30 Drums | 570 Drums | |
Total Disposal Cost | $120,000 | $6,000 | $114,000 | Reduced volume directly cuts disposal costs. |
Energy Costs (for solvent mgmt.) | Lower (no recovery process) | Higher (for recovery equipment) | Net Negative Initially | Solvent recovery systems consume energy. |
Estimated Annual Energy Cost | $5,000 | $20,000 | -$15,000 | This is an estimate; actuals depend on equipment efficiency. |
Labor Costs (for solvent mgmt.) | Moderate (handling & disposal) | Higher (operating recovery equip.) | Net Negative Initially | May require specialized labor for recovery system. |
Estimated Annual Labor Cost | $10,000 | $25,000 | -$15,000 | |
Capital Investment (Recovery System) | $0 | $250,000 (amortized over 5 years) | -$50,000 (annualized) | Capital costs for recovery equipment can be substantial but offer long-term savings. |
Annualized Equipment Cost | $0 | $50,000 | -$50,000 | |
Regulatory & Compliance Costs | Potentially Higher (due to emissions/waste) | Potentially Lower (reduced impact) | Variable | Stricter environmental regulations may favor solvent recovery. |
Estimated Annual Compliance Cost | $15,000 | $5,000 | $10,000 | Reduced waste and emissions can lead to lower compliance burdens. |
TOTAL ANNUAL ESTIMATED COSTS | $750,000 | $136,000 | $614,000 | |
Other Potential Savings/Costs | ||||
Reduced Environmental Impact | Higher Impact | Lower Impact | Qualitative Benefit | Solvent recovery promotes sustainability. |
Enhanced Supply Chain Security | Reliant on new solvent market | Less reliant, internal recycling loop | Strategic Benefit | Reduced dependence on volatile solvent market prices. |
Potential Revenue from Recycled Solvent Sales | $0 | Variable (if excess recovered solvent sold) | Potential Income | Some companies may sell high-purity recovered solvent. |
The economic argument for solvent recovery is very strong. Solvents like NMP are not cheap. In fact, they can represent a significant portion of the material costs in electrode manufacturing. When you recover and reuse, say, 95% or even more of your NMP, the savings on purchasing new solvent are immediate and substantial. Think about the volume of solvent used in a large battery plant; even a small percentage improvement makes a big difference. Beyond the direct cost of solvent, there's the cost of disposal. If you're not recovering, you're likely paying to treat or dispose of solvent-laden air or condensed waste. These costs can also be considerable, and environmental regulations are only getting stricter, meaning disposal costs are likely to rise. Furthermore, efficient solvent recovery can reduce the load on your factory's air pollution control systems, potentially lowering their operational and maintenance costs. We've worked with clients who, after installing our recovery systems, saw payback periods much shorter than initially anticipated, simply due to these compounding savings. It's an investment that directly contributes to a leaner, more profitable operation.
Breakdown of Cost Savings:
Cost Area | Impact of Solvent Recovery |
---|---|
New Solvent Purchases | Drastically Reduced (often >95% recovery rate) |
Waste Disposal Fees | Significantly Lowered or Eliminated |
Environmental Compliance Costs | Reduced risk of fines, lower abatement needs |
Energy (Incineration) | Reduced if incineration was primary disposal method |
What Key Technologies Drive Efficient Solvent Recovery in the Battery Sector?
Curious about the science behind solvent recovery? Want to know what makes these systems effective? The right technology choice is essential for high performance.
Efficient solvent recovery in battery production primarily relies on technologies like condensation, adsorption (using activated carbon or molecular sieves), and distillation. Often, a combination of these methods provides the highest recovery rates and purity levels.
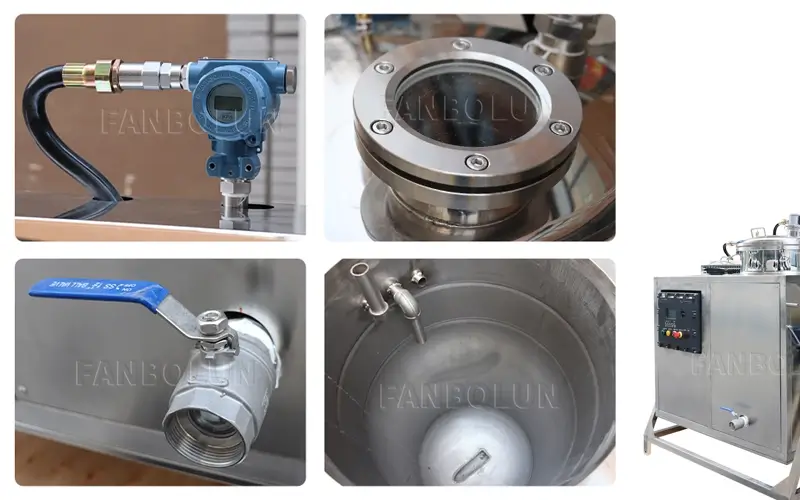
Several core technologies are employed in our solvent recovery systems, tailored to the specific needs of battery manufacturers. The first line of attack is often condensation. The hot, solvent-laden air from the drying ovens is cooled, causing the solvent vapor to condense into a liquid. This is effective for bulk recovery but might not achieve the very high purity needed for direct reuse. That's where adsorption comes in. Materials like activated carbon or specialized molecular sieves have a high affinity for solvent molecules. The exhaust stream, after initial condensation, can be passed through beds of these adsorbents, which trap the remaining solvent. The solvent can then be recovered from the adsorbent material, typically using steam or hot inert gas, in a process called desorption. Finally, distillation is often used to purify the recovered solvent. This process separates substances based on their boiling points. For NMP recovery, distillation can remove water, dissolved binder residues, and other impurities, bringing the solvent back to a quality suitable for reuse in the electrode slurry. As a manufacturer with years of R&D focus, we design integrated systems that often use these technologies in series to maximize both recovery efficiency and the purity of the reclaimed solvent, ensuring it meets the stringent requirements of battery production.
Comparing Common Recovery Methods:
Condensation: Good for high solvent concentrations, energy efficient for bulk removal.
Adsorption: Excellent for low solvent concentrations, can achieve very clean air discharge. Requires regeneration step.
Distillation: Essential for high-purity solvent, separates solvent from water and other contaminants.
How Do We Choose the Right Solvent Recovery System for Our Battery Production Line?
Facing the decision of which thinner recycler machine to invest in? Unsure about the critical factors to consider for your specific needs? Making the right choice is vital.
Choosing the right solvent recovery system involves assessing your solvent type and volume, required purity, air flow rates from dryers, available space, and integration with existing lines. Partnering with an experienced manufacturer ensures a tailored, cost-effective solution.
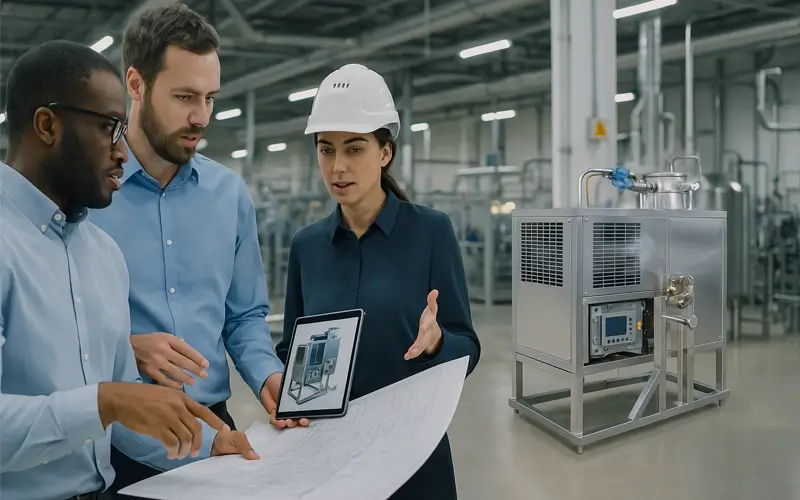
Selecting the ideal solvent recovery system for your battery production is not a one-size-fits-all decision. Several factors must be carefully evaluated. First, what is the primary solvent you're using (e.g., NMP), and what is the typical volume or concentration in your dryer exhaust? This dictates the scale and capacity of the system. Second, what level of purity is required for the recovered solvent to be reused in your process? Some applications are more tolerant than others. Third, what are the airflow characteristics of your drying ovens? The recovery system must be sized to handle this airflow effectively. Fourth, consider the physical footprint. Do you have adequate space for the equipment, including any ancillary units like chillers or distillation columns? Fifth, integration is key. How will the system interface with your existing production line and control systems? At our company, with our extensive export experience and focus on customized solutions, we work closely with clients to understand these specific parameters. We believe in transparency and technical exchange, even welcoming factory visits to see our production capabilities. Our engineers, many of whom are fluent in English, can help analyze your needs and propose a system that offers the best balance of performance, cost-effectiveness, and reliability, backed by our 24/7 after-sales support.
Key Questions to Ask Before Investing:
What is my average and peak solvent load?
What purity level do I need for reused solvent?
What are the energy consumption and operational costs?
What level of automation is required?
What kind of after-sales support and spare parts availability can I expect? (We pride ourselves on lifetime cost-price service after the warranty period).
Solvent recovery boosts savings and sustainability in battery making. It's a smart investment for a greener, more profitable future.