Butanone, also known as methyl ethyl ketone (MEK), is a vital solvent widely used in industries such as chemical manufacturing, coatings, and adhesives. Its unique chemical properties make it an indispensable tool for dissolving, cleaning, and formulating. However, like many industrial solvents, butanone comes with environmental and economic concerns if not managed effectively. Recovering and reusing butanone through advanced systems can mitigate these concerns while improving operational efficiency.
In this article, we’ll explore the significance of butanone recovery, how it integrates with solvent recycling machine, and why implementing such solutions could be the game-changer your business needs.
Why Is Butanone Recovery Important?
The rising cost of raw materials and stringent environmental regulations highlight the importance of solvent recovery. Butanone, a high-demand solvent, is no exception. Left unmanaged, butanone waste can lead to:
Increased Operational Costs: The expense of regularly purchasing virgin solvents and disposing of waste solvents can strain a company’s budget.
Environmental Concerns: Improper disposal of butanone contributes to environmental pollution and can lead to regulatory penalties.
Loss of Valuable Resources: Discarding used butanone means losing a solvent that could be recycled and reused multiple times without compromising its efficiency.
So, how can industries address these issues? The answer lies in efficient butanone recovery solutions.
What Does a Solvent Recycling System Offer?
Solvent recycling systems play a crucial role in the recovery of butanone. These systems are designed to reclaim used solvents, purify them, and make them ready for reuse. The process involves separating contaminants and impurities from the solvent through methods like distillation, filtration, and condensation.
Key benefits of integrating a solvent recycling system include:
Cost Savings: By reusing recovered butanone, industries can significantly reduce their need for fresh solvent purchases.
Sustainability: Recycling reduces solvent waste, promoting eco-friendly practices that align with global sustainability goals.
Regulatory Compliance: Many industries face strict regulations regarding solvent usage and disposal. Solvent recycling systems help ensure compliance while minimizing environmental impact.
Are there any specific challenges your industry faces with solvent waste? Advanced recycling systems are often flexible enough to adapt to unique operational needs, offering tailored solutions to different industrial applications.
The Process of Butanone Recovery
The recovery process for butanone involves several steps, typically supported by specialized equipment. Here’s how it works:
Collection: Used butanone is collected from industrial processes. This step often includes the consolidation of solvents from multiple sources within a facility.
Distillation: The collected butanone undergoes distillation, where it is heated to separate the solvent from contaminants based on boiling point differences.
Condensation: The purified butanone vapor is then cooled and condensed back into a liquid form.
Storage and Reuse: The recovered butanone is stored for reuse in the same or different processes, maintaining its chemical integrity.
What is the quality of recovered butanone compared to virgin solvent? In most cases, properly recovered butanone matches or even exceeds the performance of fresh solvent, making it an excellent alternative without compromising on results.
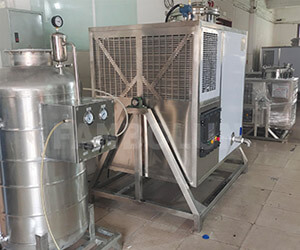
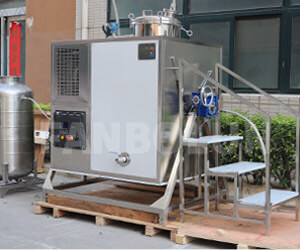
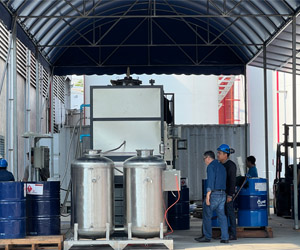
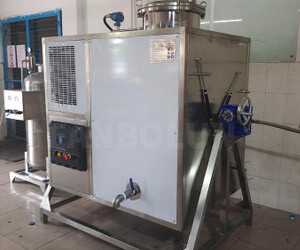
Why Should Businesses Invest in Butanone Recovery Systems?
While the initial investment in a solvent recycling system might seem significant, the long-term benefits outweigh the costs. Businesses can experience:
Enhanced Profit Margins: By reducing solvent purchase costs and lowering waste disposal expenses, profit margins improve significantly.
Operational Efficiency: Streamlined solvent management ensures uninterrupted production processes.
Improved Workplace Safety: Recovering butanone reduces the volume of hazardous waste on-site, contributing to a safer work environment.
Moreover, in industries where butanone is a primary solvent, recovery systems can provide a competitive edge by lowering production costs while meeting sustainability standards.
Tailoring Recovery Systems for Butanone
Not all recovery systems are created equal. Industries using butanone must choose solutions that cater specifically to their operational scale and requirements. Factors to consider include:
Capacity: How much solvent is used daily, and how much waste is generated?
Recovery Efficiency: Does the system maximize solvent recovery with minimal energy consumption?
Automation: Is the system user-friendly and capable of integrating with existing operations?
When selecting a recovery system, it’s essential to consult with experts who understand both the technical aspects of the equipment and the demands of your industry.
What About Other Solvents?
While this article focuses on butanone, solvent recycling systems are versatile and can recover a variety of other solvents. Many facilities combine butanone recovery with the recycling of acetone, ethanol, and other commonly used chemicals. A comprehensive solvent recycling strategy not only optimizes butanone management but enhances overall efficiency across the board.
1. Benzene solvents: such as toluene, xylene, benzene, etc. These solvents are widely used in the fields of chemical industry, coatings, paints, etc.
2. Ketone solvents: such as acetone, butanone, cyclohexanone, etc., are often used in cleaning, dissolving and diluting processes.
3. Ester solvents: such as methyl acetate, ethyl acetate, n-butyl acetate, etc., have good solubility and volatility, and are often used in coatings, inks and other industries.
4. Halogenated hydrocarbon solvents: such as dichloromethane, trichloroethylene, tetrachloroethylene, etc. These solvents have important applications in electronics, metal processing and other industries.
5. Alcohol solvents: such as methanol, ethanol, isopropanol, etc., are widely used in chemical industry, medicine, coatings and other fields.
6. Other organic solvents: such as ether, cyclohexane, alkanes, plate washing water, car washing water, anti-white water, white gasoline, 200# solvent oil, volatile oil, fin oil, aviation kerosene, D40-D-60 solvent oil, hydrocarbon cleaning agent, thinner, thinner and other mixed solvents and other organic solvents not listed.
The types of solvents listed above are only some examples, not all. In actual applications, the T-60 solvent reclaimer may also be able to recover other types of organic solvents. Therefore, when choosing to use this equipment, it is recommended to consult and confirm in detail according to the specific solvent type and recovery requirements.
What’s Next for Your Facility?
Is your facility fully equipped to handle the challenges of solvent waste? If butanone is a core part of your operations, it’s time to consider a recovery solution that reduces costs, enhances sustainability, and ensures compliance with regulations.
Solvent recycling systems are an investment in the future of your business, offering long-term savings and operational benefits. By recovering butanone and other solvents, companies can take a significant step toward achieving their environmental and economic goals.
Why wait to implement these solutions? The benefits are clear, the technology is available, and the savings start from day one. It’s time to unlock the potential of butanone recovery and position your business for success in a rapidly evolving industrial landscape.
Are you ready to explore tailored solutions for butanone recovery? Partner with experts to design a system that meets your unique needs, boosts profitability, and sets the foundation for a sustainable future.