Are high solvent costs and environmental concerns weighing down your pharmaceutical operations? This pressure can stifle growth and complicate compliance. Solvent recovery offers a clear path forward.
Solvent recovery transforms pharmaceutical production by drastically cutting raw material expenses through solvent reuse, minimizing hazardous waste for better environmental compliance, and ensuring a stable supply of high-purity solvents crucial for drug quality and manufacturing consistency.
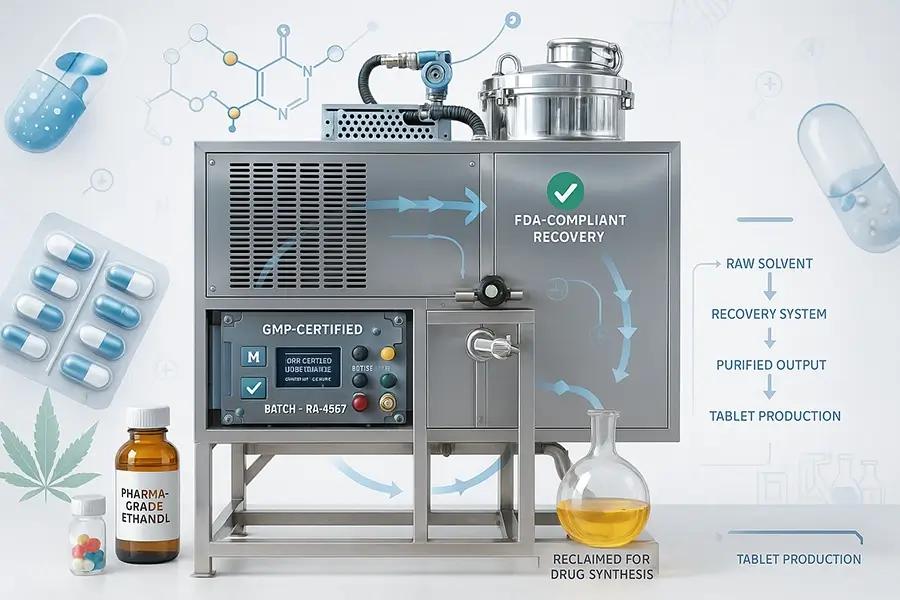
As a company, Zhengzhou Keda, with over 16 years dedicated to laboratory and production equipment, we've seen firsthand how vital efficient processes are. In the pharmaceutical world, where precision and purity are everything, managing resources like solvents isn't just about cost-saving; it's about quality and responsibility. I want to share some insights into how embracing solvent recovery can be a truly transformative step for your operations, based on what we've learned and the solutions we provide.
Why Is Effective Solvent Recovery a Game-Changer for Pharmaceutical Companies?
Struggling with escalating solvent purchase prices and strict environmental disposal regulations? These challenges directly hit your profit margins and sustainability reports. Effective solvent recovery provides a powerful, practical solution.
Effective solvent recovery is a game-changer because it significantly cuts operational costs by recycling valuable solvents, reduces environmental liabilities by minimizing hazardous waste, and enhances supply chain security for critical pharmaceutical manufacturing inputs.
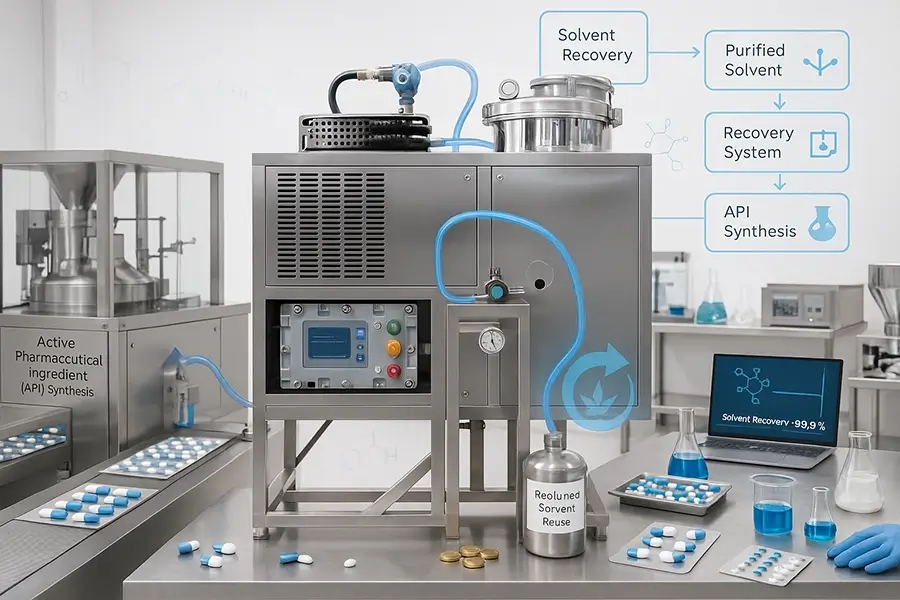
For any pharmaceutical company, the drive for efficiency and sustainability is constant. Solvents are essential but also represent a significant operational expense and a potential environmental headache. Let's look deeper into why tackling this makes such a difference. I remember working with a mid-sized pharmaceutical firm that was spending a fortune annually on virgin solvents and even more on their disposal. The change was remarkable once they integrated a recovery system.
The Economic Edge: Slashing Solvent Expenses
The most immediate benefit is financial. Solvents, especially high-purity grades required in pharma, are expensive. Recovering and reusing them, even with a recovery rate of 90-98% which our machines often achieve, means a dramatic reduction in new solvent purchases. Think about the annual volume of solvents like ethanol, methanol, or acetone you use. Cutting that by a large percentage directly impacts your cost of goods sold. The return on investment (ROI) for a solvent recovery machine can often be seen in months, not years. It's not just savings; it's redirecting capital to other critical areas like R&D.
Expense Area | Without Solvent Recovery (Annual Estimate) | With Solvent Recovery (Annual Estimate) | Potential Annual Savings |
---|---|---|---|
New Solvent Purchase | $200,000 | $20,000 (assuming 90% recovery) | $180,000 |
Waste Disposal Costs | $50,000 | $5,000 | $45,000 |
Total Operational Costs | $250,000 | $25,000 | $225,000 |
Greener Pharma: Meeting Environmental Mandates
Environmental regulations are only getting tighter. The pharmaceutical industry, by its nature, can generate significant hazardous waste if solvents aren't managed properly. Solvent recovery is a cornerstone of green chemistry and sustainable manufacturing. By reducing the volume of solvent waste sent for incineration or other disposal methods, you cut down on emissions, reduce your carbon footprint, and lessen your environmental liability. This isn't just good for the planet; it boosts your company's reputation and makes it easier to comply with ISO 14001 and other environmental standards. We've helped many clients turn their waste streams into valuable assets, which is always a satisfying outcome.
Operational Stability: Ensuring Supply Chain Resilience
Relying on external suppliers for 100% of your solvent needs can expose you to price volatility and supply chain disruptions. By recovering and reusing solvents in-house, you create a more closed-loop system. This internal sourcing provides a buffer against market fluctuations and ensures that a significant portion of your solvent requirement is always on hand. This was particularly evident during recent global supply chain challenges; companies with robust recovery systems were less affected. It's about taking control of a critical part of your production process.
How Does a Solvent Recovery Machine Actually Work to Purify Solvents?
Ever wondered how dirty, used solvents can be transformed back into high-purity liquids, ready for reuse? The technology might seem complex, but the underlying principles are elegantly simple and highly effective.
Solvent recovery machines primarily use distillation. They heat the contaminated solvent to create vapor, leave impurities behind, and then cool the vapor to condense it back into a purified liquid solvent, ready for reuse.
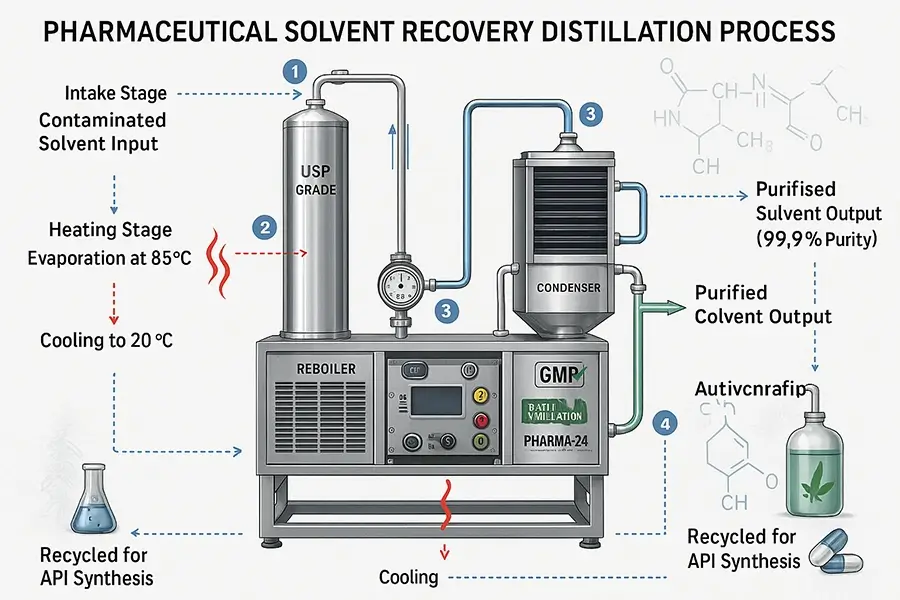
Understanding the "how" is key to appreciating the value. At ZZKD, we've spent years refining our solvent recovery systems, like our rotary evaporators and specialized distillation units, to make them efficient and user-friendly. Let me walk you through the basic process, which is quite fascinating. It's a bit like making coffee, where you extract the good stuff and leave the grounds behind, but with more precise temperature and pressure controls.
The Heart of the Matter: Distillation Explained Simply
The most common method for solvent recovery is distillation. This process relies on the fact that different substances have different boiling points. Here's a simplified breakdown:
Heating: The used solvent (a mixture of the pure solvent and contaminants like oils, resins, pigments, etc.) is placed in a boiling chamber. Our machines apply controlled heat, often under vacuum to lower the solvent's boiling point, making the process safer and more energy-efficient.
Vaporization: As the mixture heats, the solvent, having a lower boiling point than most contaminants, turns into a vapor. The heavier contaminants remain behind in the boiling chamber as residue.
Separation: The solvent vapor travels away from the boiling chamber, leaving the concentrated waste.
Condensation: This vapor then passes through a condenser. The condenser is cooled (using water or a chiller system), causing the solvent vapor to cool down and turn back into a liquid – now in a much purer form.
Collection: The purified liquid solvent is collected in a separate, clean tank, ready to be analyzed for purity and reused in your processes.
This process can recover a very high percentage of the original solvent, often exceeding 95% purity, depending on the initial solvent and contamination type. It's a physical separation, so it doesn't alter the chemical properties of the solvent itself.
Key Components of Our Solvent Recovery Systems
While the principle is simple, the equipment needs to be robust and precise. Our solvent recovery machines typically include:
Boiling Tank/Chamber: Often made of stainless steel, this is where the initial heating and vaporization occur. For some applications, like with our glass reactors or rotary evaporators, glass is used for visibility and chemical resistance.
Heating System: This could be an oil bath, heating jacket, or steam, designed for even and controlled temperature increase.
Vacuum System (Optional but common): A vacuum pump reduces the pressure inside the system, lowering the solvent's boiling point. This saves energy and is crucial for heat-sensitive solvents.
Condenser: A series of coils or plates where the solvent vapor is cooled and liquefied. Efficient cooling is key to high recovery rates.
Collection Tank(s): For storing the purified solvent and sometimes for the waste residue.
Control Panel: Allows operators to set and monitor parameters like temperature, vacuum level, and processing time. Modern systems, like ours, often feature automation for ease of use and safety.
We design these components to work together seamlessly, ensuring safety, efficiency, and high-purity output for our clients in the pharmaceutical sector.
What Key Factors Should You Consider Before Investing in a Solvent Recovery System?
Thinking about a solvent recovery system but feeling overwhelmed by the options and technical details? Choosing the right one is crucial for success. Let's break down the essentials for making an informed decision.
Key factors include the types and volumes of solvents used, required purity levels for reuse, operational safety features (especially for flammable solvents), system capacity and throughput, automation level, and the total cost of ownership beyond the initial purchase price.

Investing in a solvent recovery system is a significant decision, but one that can bring substantial returns. From my experience at Zhengzhou Keda, helping countless clients select the right equipment, the process becomes much simpler if you ask the right questions upfront. It's not just about buying a machine; it's about integrating a solution that fits your specific pharmaceutical processes.
Matching the Machine to Your Solvents
Not all solvents are created equal, and neither are recovery systems. You need to consider:
Type of Solvents: Are they flammable (e.g., ethanol, IPA, hexane)? Corrosive? What are their boiling points? This will dictate material compatibility (stainless steel, glass-lined) and safety features (explosion-proof design).
Contaminants: What are you trying to separate the solvent from? Solids, oils, water, other chemicals? The nature of the contamination affects the distillation process and potential pre-treatment needs.
Volume and Frequency: How much solvent do you need to recover per day or per batch? This will determine the required capacity (e.g., 50L, 100L, 200L per batch) and whether a batch or continuous system is more suitable.
Purity Requirements: How Clean is Clean Enough?
In pharmaceuticals, purity is paramount. You need to define the required purity level of the recovered solvent for its intended reuse. Can it be used for initial cleaning, or does it need to meet USP grade for direct product contact? This might influence the type of distillation (e.g., fractional distillation for separating solvents with close boiling points) and whether post-treatment or polishing steps are needed. We often recommend clients test the recovered solvent to ensure it meets their specific quality control standards. As a manufacturer, we can guide you on the expected purity from our machines based on your input solvent.
Safety First: Essential Features for Pharma Environments
Safety is non-negotiable, especially when dealing with flammable or hazardous solvents. Look for systems with:
Explosion-proof (ATEX rated where necessary) components: Motors, heaters, control panels.
Automatic shutdown features: For over-temperature, over-pressure, or system malfunctions.
Proper ventilation and vapor handling.
Robust construction and leak prevention.
Certifications: CE marking is standard for us, indicating compliance with European safety standards. ISO9001 shows our commitment to quality management.
Beyond the Price Tag: Total Cost of Ownership (TCO)
The initial purchase price is just one part of the equation. Consider the TCO:
Energy Consumption: Efficient systems use less power.
Maintenance Requirements: How easy is it to clean and maintain? Availability of spare parts? We pride ourselves on robust design and readily available support.
Operator Time: Automated systems require less manual intervention.
Installation and Training: We offer support to ensure your team can operate the equipment safely and effectively.
Lifespan of the Equipment and Warranty: A well-built machine will serve you for many years. We offer a one-year warranty and lifetime cost-price service.
I always advise potential clients to discuss these points thoroughly. A slightly more expensive machine upfront might save you significantly in the long run through lower operating costs and higher reliability. Our 24/7 after-sales support team is a testament to our commitment to long-term customer satisfaction.
Consideration Factor | Key Questions to Ask | Why It Matters |
---|---|---|
Solvent Profile | What types? Flammable? Corrosive? Boiling points? | Dictates machine materials, safety features, process parameters. |
Volume & Throughput | How much solvent per batch/day? Batch or continuous? | Ensures capacity meets production needs without bottlenecks. |
Purity Specification | Required purity for reuse? Any specific standards (USP)? | Determines if standard distillation is enough or if advanced techniques are needed. |
Safety Standards | Need for explosion-proof design? Automation for safety interlocks? | Critical for personnel safety and regulatory compliance. |
Footprint & Utilities | Space available? Power, cooling water, compressed air requirements? | Practical installation and operational feasibility. |
Vendor Support & TCO | Warranty, after-sales service, spare parts, energy efficiency? | Long-term reliability, operational costs, and peace of mind. |
In summary, solvent recovery offers clear financial, environmental, and operational advantages, making it a vital technology for modern pharmaceutical production. We're here to help you find the best solution.