Tired of high solvent disposal costs and environmental worries? These expenses drain your budget and impact our planet. Imagine cutting those costs significantly.
Yes, absolutely! Solvents can be effectively recycled. Modern solvent recovery machines, like the ones we've specialized in at Zhengzhou Keda for over 16 years, make it easy to reclaim and reuse valuable solvents right in your facility, saving money and protecting the environment.
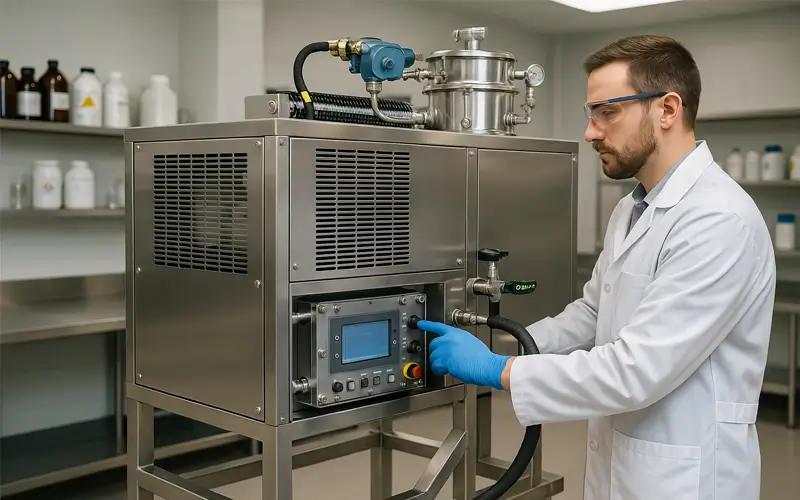
As a manufacturer deeply involved in international markets, we've seen firsthand how essential efficient resource management is. Recycling solvents isn't just a trend; it's a practical step towards smarter operations. Let me share some insights into why this is crucial and how it works, based on our extensive experience exporting these systems to 87 countries.
Why should my business care about recycling solvents?
Are solvent expenses eating into your profits? Disposing of used solvents is costly and impacts our environment. What if you could reduce both burdens effectively?
Recycling solvents directly benefits your business by significantly cutting down on new solvent purchase and waste disposal costs. It also helps reduce your environmental impact and demonstrates a commitment to sustainability, a factor increasingly valued by customers and stakeholders.
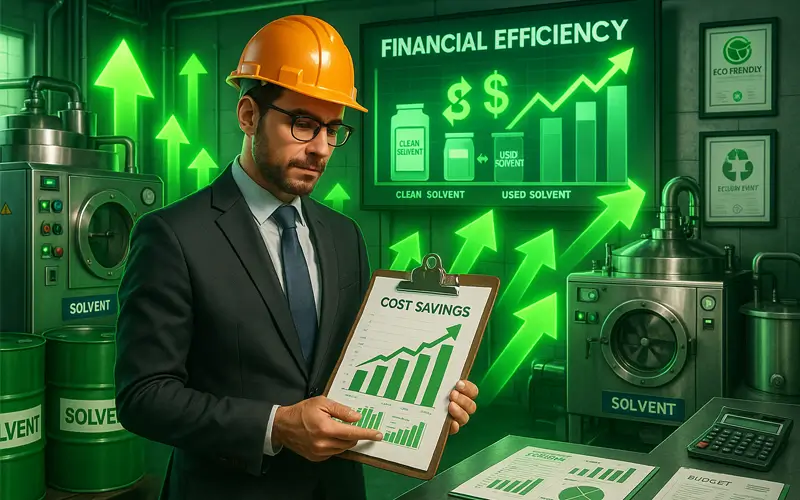
From my perspective, after 16 years dedicated to laboratory and industrial equipment, the reasons businesses turn to solvent recycling are clear and compelling. It’s not just about being "green"; it's about smart business.
Reducing Your Operational Costs
Think about this: every liter of solvent you recycle is a liter you don't have to buy. For many companies, especially in the chemical, pharmaceutical, and manufacturing sectors we serve, new solvent purchases represent a significant recurring expense. Then there are the disposal fees for hazardous waste, which are always on the rise. Our solvent recovery machines can typically recover 95% or more of used solvents, leading to a drastic reduction in both these costs. I recall a client in the printing industry who cut their solvent spending by nearly 70% within the first year of installing one of our systems. That's a direct boost to the bottom line.
Enhancing Your Environmental Responsibility
Today, corporate social responsibility isn't just a buzzword; it's a necessity. Customers, especially in international markets, are increasingly scrutinizing the environmental practices of their suppliers. By recycling solvents, you minimize hazardous waste generation and reduce the carbon footprint associated with producing new solvents and transporting waste. Our equipment, built to meet ISO9001 and CE standards, ensures that you're using reliable, internationally recognized technology to achieve these environmental goals. It's about aligning your operations with "Made in China + International Quality."
Improving Workplace Safety and Compliance
Handling and storing large quantities of waste solvents, and arranging for their transport, carries inherent risks. Recycling in-house reduces the volume of hazardous materials on site and minimizes the need for off-site transportation. This can lead to a safer working environment for your employees. Furthermore, environmental regulations are becoming stricter globally. Having an effective solvent recycling program helps ensure you stay compliant, avoiding potential fines and reputational damage. We design our machines with user safety as a priority, incorporating features that simplify operation and maintenance.
How exactly do solvent recovery machines make recycling possible?
Does the idea of solvent recycling seem complex or overly technical? You might think it requires complicated chemical processes. But it's actually much simpler than you imagine with the right equipment.
Solvent recovery machines primarily use a process called distillation to separate valuable solvents from contaminants. The machine heats the used solvent mixture until the solvent evaporates, leaves the impurities behind, and then cools the solvent vapor to condense it back into a pure, reusable liquid form.
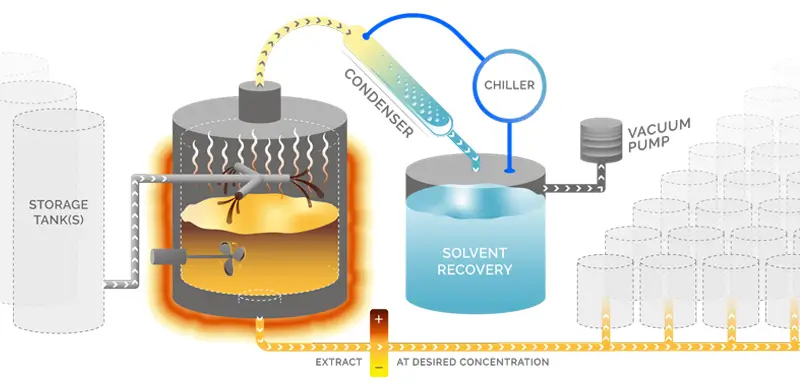
As specialists in manufacturing extraction and distillation equipment, we at Zhengzhou Keda have refined this process over many years. Let me break it down further. It's a technology we've successfully exported and supported globally, so we know how to make it work efficiently for diverse applications.
The Distillation Process Explained Simply
Imagine you have saltwater and you want fresh water. If you boil the saltwater, the water turns into steam, leaving the salt behind. If you then collect and cool that steam, you get pure water. Solvent recycling works on a very similar principle. Here are the basic steps our machines automate:
Heating: The contaminated solvent is placed in a distillation tank and gently heated. The heating is carefully controlled to reach the solvent's boiling point but not that of most contaminants.
Vaporization: The pure solvent turns into vapor.
Separation: The heavier contaminants, like oils, resins, pigments, and greases, do not evaporate easily and remain in the tank as residue.
Condensation: The solvent vapor is directed to a condenser, which cools it down, causing it to turn back into a liquid. This liquid is now clean, purified solvent.
Collection: The clean solvent is collected in a separate container, ready for reuse. The waste residue is concentrated and significantly reduced in volume, making its disposal easier and cheaper.
Key Components of Our Solvent Recovery Machines
Our solvent recovery machines are designed for reliability and ease of use. Key components include a robust distillation tank (often made from stainless steel for chemical resistance), a precisely controlled heating system (electric or steam), an efficient cooling system for condensation (air-cooled or water-cooled options are common), and a user-friendly control panel. We leverage our R&D to ensure these components work seamlessly together. For instance, our temperature control units are critical for achieving optimal separation. We have continuously innovated these systems based on feedback from our international clients and our 16 years of manufacturing experience.
Customization: Not a One-Size-Fits-All Approach
We understand that different industries and applications have unique needs. The type of solvent, the nature of contaminants, the volume to be processed, and required purity levels all vary. That's why we don't just sell off-the-shelf machines. We offer "customized, high-cost-performance equipment." This might involve selecting specific materials of construction, sizing the machine appropriately, or incorporating features like vacuum distillation for high-boiling point solvents or solvents sensitive to heat. Our engineers, many of whom are fluent in English, work closely with clients to determine the best configuration.
Which common industrial solvents can I actually recycle with a machine?
Worried if your specific solvents can be effectively recycled? Many businesses use a diverse range of solvents and understandably face this uncertainty. What if yours are perfectly suitable for recovery?
A wide variety of common industrial solvents are highly recyclable! This includes alcohols (like ethanol, IPA), ketones (acetone, MEK), esters (ethyl acetate), aromatic hydrocarbons (toluene, xylene), aliphatic hydrocarbons, and many cleaning solvents and thinners. Our machines handle an extensive range.
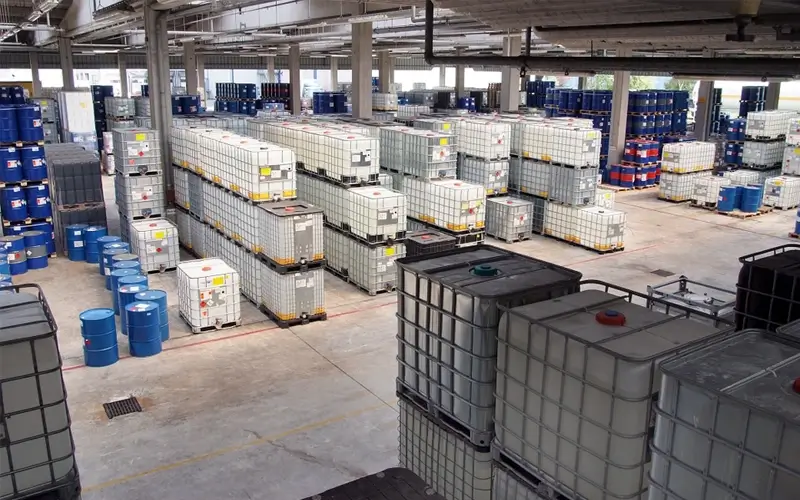
Over our years of exporting to 87 countries, we've seen our solvent recovery machines successfully used across a multitude of industries, each with its own preferred solvents. The good news is that the list of recyclable solvents is quite long.
Examples of Commonly Recycled Solvents:
Here's a table illustrating some solvent types and their typical applications where recycling is beneficial:
Solvent Category | Examples | Common Industries/Applications |
---|---|---|
Alcohols | Ethanol, Isopropyl Alcohol (IPA), Methanol | Printing, Pharmaceuticals, Electronics Cleaning, Disinfectants |
Ketones | Acetone, Methyl Ethyl Ketone (MEK) | Paints & Coatings, Adhesives, Fiberglass Production, Degreasing |
Esters | Ethyl Acetate, Butyl Acetate | Inks, Coatings, Adhesives, Chemical Synthesis |
Aromatic Hydrocarbons | Toluene, Xylene | Paints, Thinners, Adhesives, Chemical Manufacturing |
Aliphatic Hydrocarbons | Heptane, Hexane, Mineral Spirits | Cleaning Agents, Degreasers, Extraction Processes |
Chlorinated Solvents (some types) | Methylene Chloride (DCM), Perchloroethylene | Degreasing, Dry Cleaning (use requires careful handling & specific machine designs) |
Specialty Blends | Paint thinners, Gun wash, Cleaning blends | Automotive Refinishing, Manufacturing, Printing |
This is not an exhaustive list, but it gives you an idea of the versatility. The primary requirement is that the solvent has a boiling point distinct from its contaminants and doesn't decompose at its boiling temperature.
Factors We Consider for Recyclability
When a client asks if their solvent can be recycled, we typically look at its boiling point, the types of contaminants (e.g., solids, oils, water), and whether it forms azeotropes (mixtures that boil at a constant temperature without changing composition). While azeotropes can be more complex, some can still be managed with specific distillation techniques. Our machines can often be adjusted, for example, by using vacuum distillation to lower the boiling point of thermally sensitive solvents.
Consult with Us – We Welcome Technical Exchange
As a manufacturer, we believe in "technical exchange." If you're unsure about your specific solvent or waste stream, we encourage you to reach out. We can often assess its suitability for recycling based on its properties or even suggest a small trial. This is part of our commitment to providing effective solutions for our customers, drawing on our 16 years of manufacturing and R&D in this field.
What are the real cost savings when I recycle solvents in-house?
Are you looking for clear, tangible financial benefits from your investments? Solvent costs can be a significant operational burden. Imagine turning that recurring expense into substantial savings for your company.
In-house solvent recycling offers very real and substantial cost savings. You will dramatically cut spending on new solvent purchases and significantly reduce waste disposal fees, often leading to a quick return on investment for the recovery equipment.
Liters Used/Month | Cost/Liter | New Solvent Cost | Drums Disposed | Disposal Cost/Dr | Total Disposal Cost | Total Monthly Cost | Recovery Rate | Saved Solvent Cost | Saved Disposal Cost | Total Savings | New Total Cost |
---|---|---|---|---|---|---|---|---|---|---|---|
1,000 | $5 | $5,000 | 5 | $200 | $1,000 | $6,000 | 95% | $4,750 | $800* | $5,550 | $450 |
800 | $6 | $4,800 | 4 | $200 | $800 | $5,600 | 90% | $4,320 | $600 | $4,920 | $680 |
1,500 | $4 | $6,000 | 8† | $200 | $1,600 | $7,600 | 80% | $4,800 | $1,200 | $6,000 | $1,600 |
From our extensive experience as exporters, we've seen companies recoup the investment in a solvent recovery machine surprisingly quickly – sometimes in less than a year. The financial argument is usually very strong, especially for businesses that use moderate to high volumes of solvents.
Calculating Your Return on Investment (ROI)
To understand the potential savings, consider these key factors:
Cost of New Solvent: How much do you pay per liter or gallon for fresh solvent?
Volume of Solvent Used: How much solvent do you consume monthly or annually?
Cost of Waste Disposal: What are your current expenses for disposing of used solvent (including transport, permits, and disposal fees per drum/container)?
Recovery Rate: Our machines typically achieve high recovery rates (e.g., 90-98%). This tells you how much of your used solvent can be reclaimed.
Machine Operating Costs: These are usually minimal, mainly electricity and occasional maintenance.
Let's say you use 1000 liters of solvent per month, costing $5 per liter. That's $5,000/month for new solvent. If disposal costs $200 per 200-liter drum, and you dispose of 5 drums, that's another $1,000. Total: $6,000/month. If a machine recovers 95% of this, you're saving close to $4,750 on new solvent and significantly on disposal. The machine pays for itself rapidly.
Drastic Reduction in New Solvent Purchases
This is the most direct saving. If you recover 95% of your solvent, you only need to purchase 5% of your previous volume as make-up solvent to replace losses during processes or the small unrecoverable portion. This alone can lead to massive savings, as I mentioned earlier. It's a consistent, month-after-month benefit.
Lower Waste Disposal Fees
Hazardous waste disposal is not only expensive but also heavily regulated. By recycling solvents, the volume of hazardous waste you need to dispose of is dramatically reduced – often by 90% or more. The residue left in the machine is typically a concentrated sludge, much smaller in volume and sometimes even classifiable as non-hazardous, further reducing disposal costs. This also means less paperwork and fewer compliance headaches.
Long-Term Value and Reliability
Our commitment as Zhengzhou Keda includes providing durable equipment. We offer a "lifetime cost-price service" for parts and maintenance after the warranty period. This ensures your investment continues to deliver savings for many years. As a company with 16 years of continuous international export experience, we build machines designed for longevity and consistent performance because we understand the operational demands of businesses worldwide.
How do I choose the right solvent recovery system for my specific needs?
Feeling unsure about selecting the best solvent recycler for your operations? With various options available, choosing the right one can seem daunting. How do you find the perfect fit that matches your requirements?
Choosing the right solvent recovery system involves carefully assessing your specific solvent types, the daily or batch volume you need to process, the nature and level of contamination, and the required purity of the recovered solvent. We help you match these needs with the ideal machine specifications.
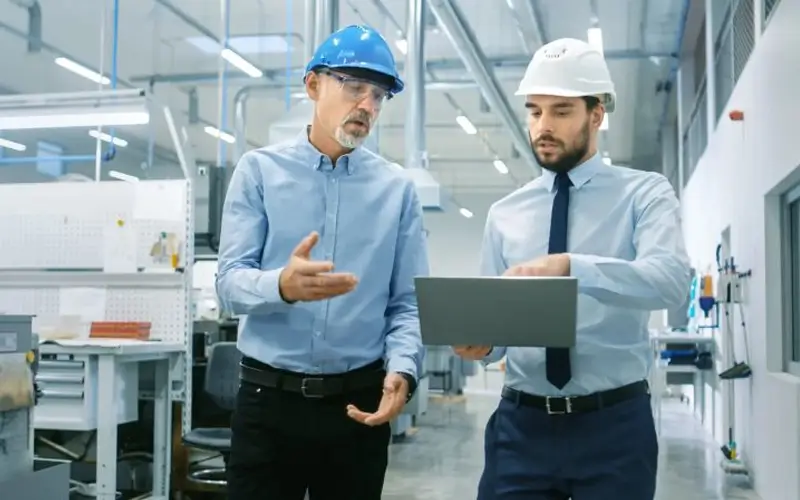
As a manufacturer that has guided countless businesses through this selection process, I can tell you that a little bit of upfront assessment goes a long way in ensuring you get a system that truly meets your needs and delivers the best value. We don't just want to sell a machine; we want to provide a solution.
Step 1: Assess Your Solvent Usage and Waste Stream
Before looking at machines, understand your own process:
What type(s) of solvents do you use? (e.g., acetone, IPA, toluene, mixed thinners). Are they flammable? What are their boiling points?
What is the typical volume of waste solvent generated per day, week, or batch? This will determine the required capacity of the recycler (e.g., liters or gallons per cycle/day).
What are the main contaminants? (e.g., paint, resin, oil, water, particulate matter). The nature and amount of contamination can influence the type of distillation (atmospheric or vacuum) and pre-filtration needed.
What purity level is required for the recycled solvent? Does it need to be ultra-pure, or is a slightly lower purity acceptable for your application (e.g., for initial cleaning tasks)?
Step 2: Understand Key Machine Specifications and Features
Once you know your needs, you can evaluate machine options based on:
Capacity: Batch capacity (e.g., 20L, 50L, 100L, up to several hundred liters for larger models) or continuous processing rate.
Distillation Method: Atmospheric distillation is common for many solvents. Vacuum distillation is used for high-boiling point solvents, heat-sensitive solvents, or to achieve better separation from certain contaminants.
Automation Level: From manual-fill/manual-empty to fully automatic systems with auto-fill, auto-discharge, and self-cleaning features.
Safety Features: Essential for flammable solvents. Look for explosion-proof ratings (e.g., ATEX, Class I Div 1), over-temperature protection, pressure relief valves. Our machines are CE certified, indicating compliance with European safety standards.
Construction Materials: Stainless steel (e.g., SUS304, SUS316L) is common for wetted parts to resist corrosion.
Cooling System: Air-cooled or water-cooled condensers. Air-cooled is simpler but may be less efficient in very hot environments.
Step 3: Why Partner with an Experienced Manufacturer like Us?
Choosing a supplier is as important as choosing the machine. At Zhengzhou Keda, we bring over 16 years of manufacturing and international export experience. What does this mean for you?
Expert Guidance: With over 50% of our engineers fluent in English, we can discuss your technical requirements clearly and provide tailored advice.
Quality Assurance: Our ISO9001 certification reflects our commitment to quality management in R&D, production, and sales.
Customization Capability: We are not just resellers. We research, develop, and produce. This means we can often customize equipment to your unique situation.
Reliable After-Sales Support: We were the first in China in our field to establish a 24/7 after-sales support team. We understand that minimizing downtime is critical, especially for our international clients.
Proven Track Record: Our products are exported to 87 countries, and we've participated in 15 international exhibitions. This global footprint is built on trust and performance.
We welcome factory visits and technical discussions to help you make an informed decision. Our goal is to ensure you get a solvent recovery solution that works efficiently and reliably for years to come.
Recycling solvents isn't just possible; it's a smart, economical, and environmentally responsible decision. Our machines at Zhengzhou Keda make it easy and efficient for your business.