Tired of soaring solvent purchase and disposal expenses eating into your profits? This constant cycle is costly and environmentally damaging, making you seek a smarter, more sustainable operational model.
By integrating a solvent recovery system, your business can recycle used solvents on-site. This cuts new solvent purchases by up to 95%, drastically reduces hazardous waste disposal fees, and aligns your operations with a profitable circular economy model, boosting both your bottom line and green credentials.
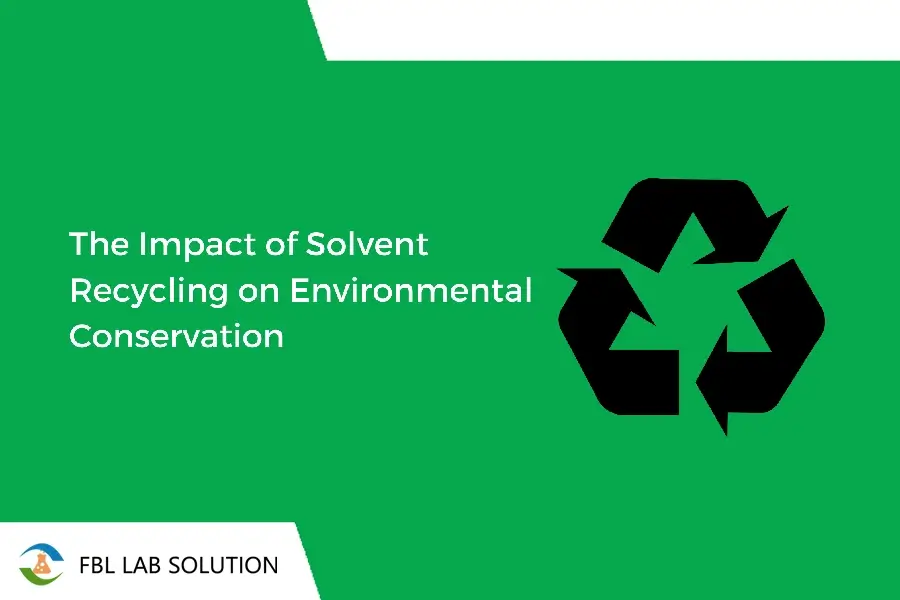
Adopting this technology is more than just an equipment upgrade; it's a fundamental shift in how you manage resources. I’ve seen firsthand how companies transform their cost structure and environmental impact almost overnight. This shift moves you from a linear "take-make-dispose" model to a circular one where resources are kept in use for as long as possible. It's about turning a liability—your waste solvent—into a valuable asset. The journey starts with understanding the tools that make this change possible.
What exactly is a solvent recovery system and how does it operate?
Confused by how a machine can turn dirty, used solvent back into pure, usable liquid? The process seems complex, leaving you unsure if it’s a viable solution for your needs.
A solvent recovery system is equipment that purifies used solvents through distillation. It heats the contaminated solvent into a vapor, leaving solid contaminants behind. The pure solvent vapor is then cooled and condensed back into a clean, reusable liquid, ready for your processes again.
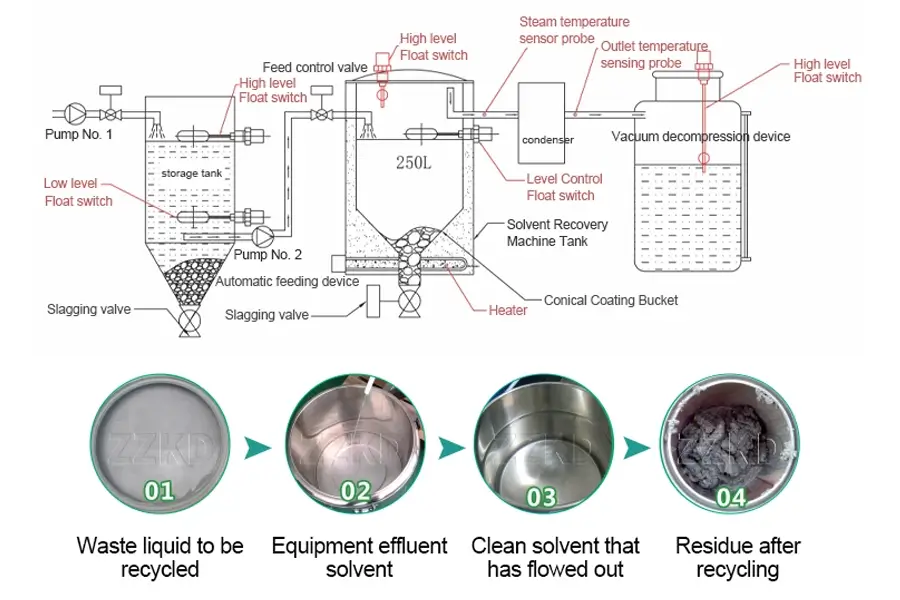
Let's dive deeper into how this technology works. From my 16 years of experience, I know that simplicity and reliability are key. The core of the system is based on a principle you might remember from high school chemistry: distillation. Different liquids have different boiling points. Solvents typically have a lower boiling point than the contaminants dissolved in them, like resins, oils, or pigments.
The Step-by-Step Process
First, the waste solvent mixture is pumped into a boiling chamber inside the machine. The system then heats this mixture under controlled conditions, often using a thermal oil jacket for even temperature distribution. As the solvent reaches its boiling point, it turns into a vapor. The heavier contaminants, which have much higher boiling points, do not vaporize and remain behind in the chamber as a sludge. This vapor then travels to a condenser, which is cooled by either air or water. Here, the vapor cools down and turns back into a high-purity liquid solvent. This clean, distilled solvent is collected in a separate tank, ready to be used again. It's a closed-loop system, which minimizes emissions and ensures a safe operating environment.
Which industries gain the most from on-site solvent recycling?
Wondering if your specific industry can truly benefit from this technology? You see the potential but need to know if it applies to your unique processes and solvent types.
Industries like chemical and pharmaceutical manufacturing, printing, automotive, and cannabis processing see immense benefits. Any operation using large volumes of solvents for cleaning, extraction, or as a process medium can significantly cut costs and improve sustainability by recycling solvents like acetone, ethanol, and IPA on-site.
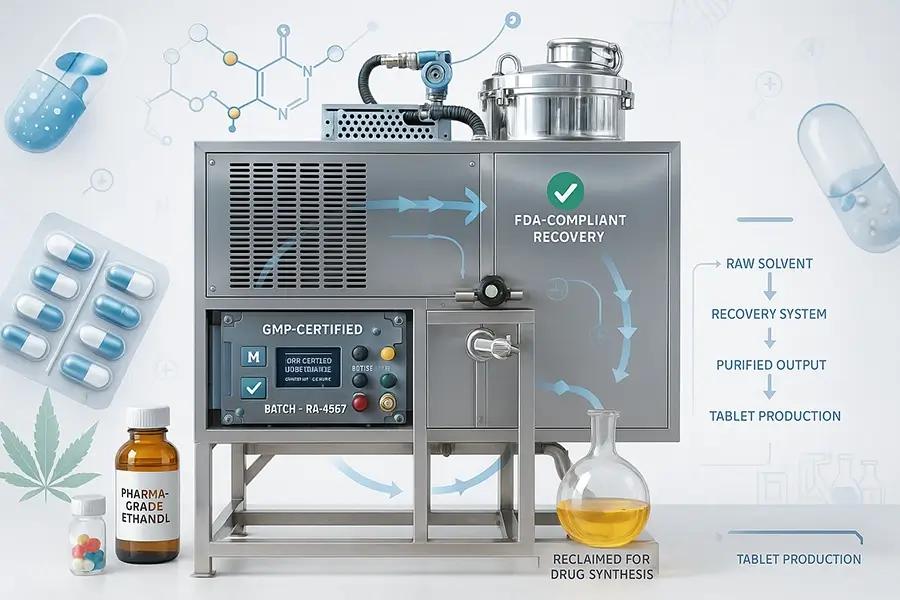
The applications for solvent recycling are incredibly broad, which is something I've seen as we've exported our equipment to 87 countries. The common thread is the use of solvents that become contaminated during a process. For example, in the printing industry, solvents are used to clean presses of ink. Instead of paying for disposal, a printing house can use an acetone recycling machine to reclaim the cleaning solvent for immediate reuse. Similarly, automotive body shops use thinners for cleaning spray guns, and they can recycle that thinner instead of constantly buying new drums. One of the biggest growth areas we've seen is in cannabis and hemp processing, where large-scale ethanol recovery is crucial for efficient and cost-effective extraction.
A Quick Look at Key Sectors
I've put together a simple table to show how different sectors use our systems. It's amazing to see the universal need for smarter resource management. The challenges might vary slightly, but the solution of recycling waste back into a usable product remains a powerful one for all these businesses.
Industry | Common Solvents Used | Primary Application |
---|---|---|
Pharmaceutical | Acetone, Methanol, IPA | Purification, Cleaning, Synthesis |
Automotive | Paint Thinner, Gun Wash | Cleaning spray guns and parts |
Printing | Toluene, Acetone, Flexo Solvents | Cleaning printing plates and rollers |
Cannabis Extraction | Ethanol, Isopropyl Alcohol | Extraction and winterization processes |
Electronics | IPA, Acetone | Cleaning circuit boards and components |
How does in-house recycling stack up against waste disposal services?
You're used to paying a service to haul away your hazardous waste. Is bringing that process in-house really better? You worry about complexity, regulations, and the initial investment.
In-house recycling offers a rapid return on investment, typically within 6-12 months, by eliminating disposal fees and new solvent costs. It gives you control over your resources, reduces regulatory paperwork for waste transport, and ensures a constant supply of clean solvent, unlike unreliable third-party services.
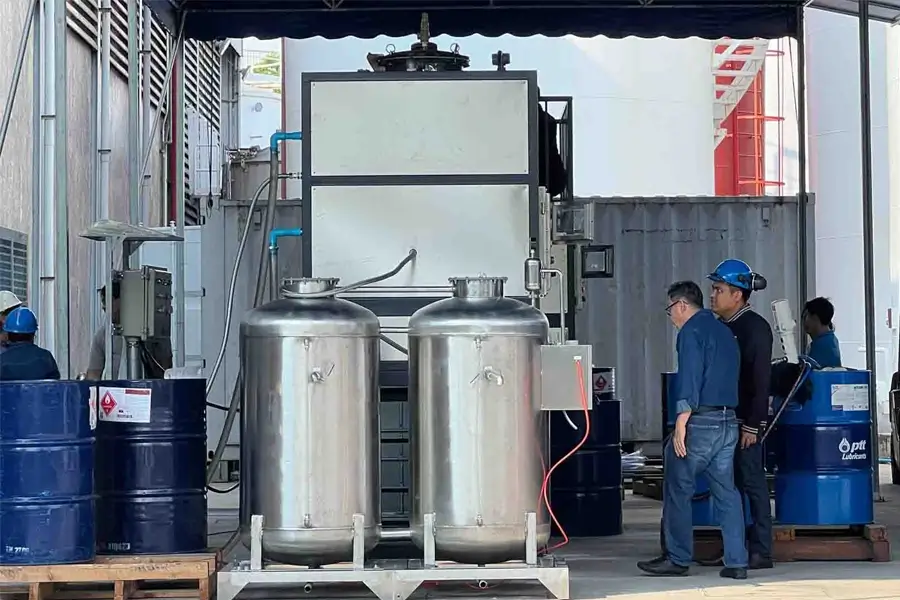
Choosing between managing your own recycling and outsourcing waste disposal is a major strategic decision. I've had countless conversations with customers about this very topic. The initial appeal of a disposal service is its simplicity: you just pay someone to make the problem disappear. However, that "disappearance" comes at a high and recurring cost. Furthermore, it completely ignores the value of the solvent you're throwing away. Proper methanol disposal, for instance, is costly, but that methanol can be easily recovered to over 99% purity. By investing in an on-site system, you are essentially buying a machine that prints money by turning your waste stream into a valuable raw material.
Cost-Benefit Analysis
The financial argument is compelling. Let's break it down. Your ongoing costs with a disposal service include the per-drum fee, transportation charges, and endless paperwork. With an in-house recycling system, your main cost is the initial capital investment. After that, the operational costs are minimal—mostly electricity. Most of our clients see a full return on their investment in less than a year. Beyond the financials, you gain independence. You are no longer subject to the price hikes or scheduling issues of a third-party vendor. You control your solvent supply, which is a huge operational advantage.
Conclusion
Embracing a circular economy with on-site solvent recycling reduces costs, ensures compliance, and powerfully demonstrates your commitment to sustainability. It's a smart, profitable, and responsible business decision.