Struggling with solvent waste? Disposing of solvents is costly and harms the environment. A dedicated machine offers an efficient, eco-friendly solution.
The best way to remove solvents efficiently and sustainably is often by using a solvent recovery machine. This equipment reclaims pure solvent for reuse, saving costs and reducing waste.
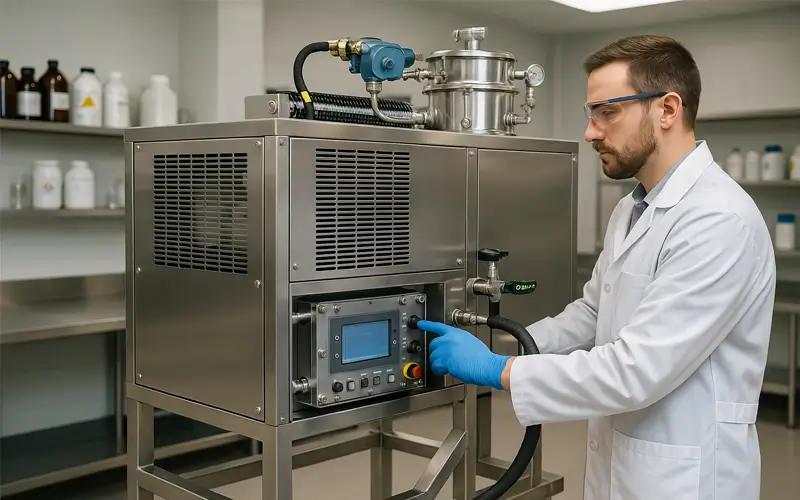
Our advanced solvent recovery systems in action.
Dealing with used solvents is a common challenge in many industries. You want a method that's not just effective but also economical and good for our planet. As someone who has been in the laboratory instrument field for over 16 years, I have seen many approaches. Let's explore the options and find what works best for your specific needs.
Why is solvent removal so important for my lab or business?
Are solvent disposal costs eating your profits? Ignoring proper solvent management can also lead to big regulatory headaches. Effective removal protects your money and our world.
Solvent removal is crucial for cost savings by reducing new solvent purchases and disposal fees. It also ensures you follow rules, keeps your workplace safe, and lessens harm to the environment.
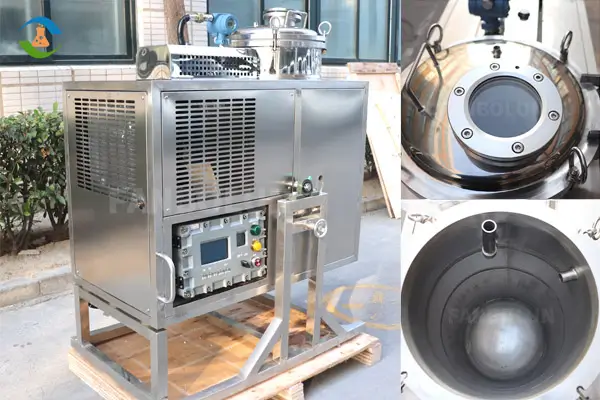
Visualizing the economic and environmental benefits.
Understanding the full impact of solvent use is key. It is not just about the task the solvent performs; it is also about what happens after. I have talked to many lab managers and business owners over the years, and the story is often similar.
The Hidden Costs of Solvents
Many people only think about the purchase price of new solvents. But the costs add up. You have to pay for the fresh solvent. Then, you often have to pay again to get rid of the used, dirty solvent. These disposal costs can include transport, special treatment, and permits. Sometimes there are environmental taxes too. I remember a client who ran a printing business. They were spending thousands each month just to have their used cleaning solvents hauled away. It was a huge drain they had not fully realized until we discussed how a solvent recovery machine could change that. We calculated they could save over 70% of those costs.
Safety and Compliance Aren't Optional
Solvents can release fumes, called Volatile Organic Compounds (VOCs). These can be harmful to people's health if they breathe them in. There are also rules and regulations about handling solvents and controlling emissions. These rules are there to protect workers and the environment. Breaking these rules can lead to fines or even stopping operations. We always say that a safe lab is a productive lab. Reducing solvent vapors is not just about following rules; it is about looking after your team and ensuring a healthy work atmosphere. My company is ISO9001 and CE certified, so we build our equipment with these safety and quality standards in mind from the start.
Protecting Our Planet, One Recovery at a Time
Solvent waste can pollute soil and water if not handled correctly. Many solvents are also made from non-renewable resources. When we recover and reuse solvents, we reduce the need to make new ones. This saves resources and cuts down on pollution. As a manufacturer that exports to 87 countries, we see a growing desire for greener solutions everywhere. That is why we focused on making equipment like solvent recovery machines. It is our way of helping our customers be more sustainable. It feels good to provide a solution that helps both the customer's budget and the planet.
What common methods are used for solvent removal today?
Using old solvent removal methods? These can be slow, not very efficient, and not kind to our earth. Let's look at modern ways that work better.
Common solvent removal methods include simple evaporation, basic distillation with lab glassware, and sending solvents off-site for disposal. Each of these has its own problems and limits.

Outlining traditional vs. modern approaches.
Over my 16 years in this industry, I have seen various approaches to solvent handling. Some are very basic, while others are more advanced. Let's look at a few common ones I encounter when talking to clients before they consider our specialized equipment.
Letting It Evaporate: The Simplest, Riskiest Way
The most basic method some try is just letting the solvent evaporate. This might happen in the open air or under a fume hood. It seems easy. However, this method means all the solvent is lost into the air. This is not good for air quality and can be a health risk. Also, you lose all that solvent, which you paid for. It is not really "removal" in a useful sense; it is more like "release." In the early days of my career, visiting some smaller workshops, I would sometimes see this. We would always advise against it due to the safety issues and the complete waste of resources. It is not a sustainable practice at all.
Basic Distillation: A Step Up, But Still Limited
A more controlled method is simple distillation using standard laboratory glassware. For example, a rotary evaporator is often used in labs to remove solvents from samples. This is much better because you can collect the evaporated solvent. However, for larger amounts of solvent waste, this becomes very slow and needs a lot of manual work. It can take a lot of time and attention from a technician. Also, the efficiency might not be very high, especially if you have mixtures of solvents. While rotary evaporators are excellent for their designed purpose – sample preparation and concentration – they are not ideal as dedicated, high-volume solvent recovery systems. We manufacture rotary evaporators too, so we understand their strengths and limitations well.
Off-Site Disposal or Recycling: Outsourcing the Problem
Many companies choose to send their used solvents to specialized waste management companies. These companies might dispose of the solvent or sometimes recycle it. This takes the problem out of your hands, which seems convenient. But, this is usually the most expensive option. You pay for the service, the transport, and you still have to buy new solvent. There are also risks with transporting hazardous waste. And, you have no control over the process once it leaves your site. I have had many conversations with customers who were shocked when they added up their yearly disposal bills. It often runs into tens of thousands of dollars for businesses with significant solvent use.
How does a solvent recovery machine offer a better solution?
Tired of high solvent costs and wasteful practices? A solvent recovery machine gives you an automatic, efficient way to clean and reuse your solvents right where you work.
A solvent recovery machine automates distillation in a safe, closed system. It efficiently separates pure solvents from dirt and waste. This means you get high-purity reusable solvent, saving much money and waste.
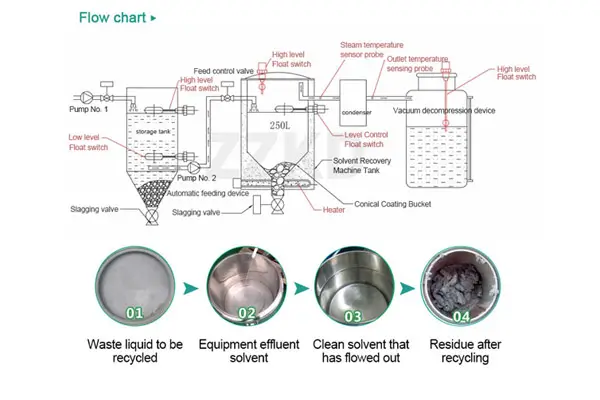
Our solvent recovery machines turn waste into value.
When I explain our solvent recovery machines, people are often keen to understand exactly how they provide a superior alternative. It is about bringing efficiency, cost-savings, and environmental responsibility directly into your own facility.
The Magic of Automated Distillation
Our solvent recovery machines work using the principle of distillation, but in a highly optimized and automated way. Here is a simple idea: the machine gently heats the dirty solvent in a controlled chamber. The pure solvent turns into vapor, leaving the dirt, residues, and contaminants behind. This clean solvent vapor then travels to a condenser, where it cools down and turns back into a liquid – now clean and ready to use again. The great part is the automation. Our machines, like the ones we have been making and improving for over 16 years at Zhengzhou Keda, are designed for easy operation. You load the waste solvent, set the parameters on a user-friendly control panel, and press start. The machine does the rest. It also has safety features like precise temperature control and pressure relief systems, all within a closed-loop system that prevents fumes from escaping. It is much safer and more efficient than open or manual systems.
Purity Matters: Getting Your Solvents Back Clean
A common question I get is about the quality of the recovered solvent. "Is it really clean enough to use again?" The answer is a strong yes for most applications. Our solvent recovery machines can typically recover solvents to a very high purity, often 95% or even higher, depending on the initial contamination and the specific solvent. This means the recovered solvent can be reused in the same processes it was originally used for, whether it's cleaning, degreasing, extraction, or in chemical reactions. We have customers in pharmaceutical, chemical, and manufacturing industries who successfully reuse their solvents daily, maintaining their product quality. For example, a company processing natural extracts can recover their ethanol, or a paint shop can reclaim their cleaning thinners. We design our machines to ensure the reclaimed solvent meets the needs of these demanding applications.
Economic and Environmental Wins Rolled into One
The financial benefits are usually very clear. By recovering and reusing solvents, you drastically cut down on the amount of new solvent you need to buy. You also save a lot on disposal costs. We often help customers calculate their return on investment (ROI). For many, the machine pays for itself in a surprisingly short time, sometimes in less than a year, especially if they use a lot of solvent. I recall a client in the electronics industry who reduced their solvent purchase by 80% and eliminated nearly all their disposal costs. Beyond the money, there is a big environmental win. Reusing solvents means less demand for new solvent production, which often involves energy-intensive processes and uses raw materials. It also means far less hazardous waste going to landfills or incinerators. As an exporter, we see that this commitment to reducing environmental footprint is becoming a global standard, and our machines help companies achieve these green goals.
What should I look for when choosing a solvent recovery machine?
Ready for a solvent recovery machine but not sure what to pick? Choosing the wrong one can lead to poor results or not fit your needs. Get the key features right.
When choosing a solvent recovery machine, think about its size (capacity), the types of solvents it can handle, how much solvent it recovers (recovery rate), safety features, how easy it is to use and maintain, and the support you get from the supplier.
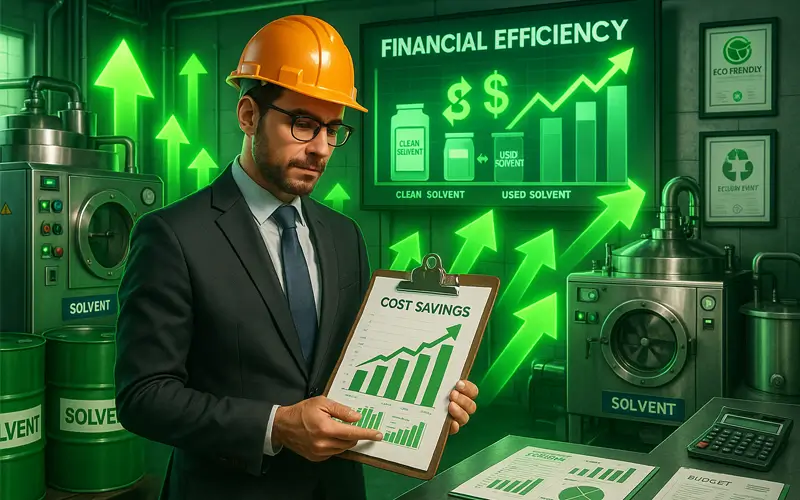
Key considerations for your investment.
Selecting the right solvent recovery machine is an important decision. It is an investment that should serve you well for years. Based on my experience helping thousands of customers worldwide, here are the main things I advise them to consider.
Matching Capacity to Your Needs
First, think about how much waste solvent you generate. Solvent recovery machines come in different sizes, usually defined by their batch processing capacity (e.g., 20 liters, 50 liters, 100 liters, or even larger per cycle). You need a machine that can comfortably handle your daily or weekly volume without being too large (which would be inefficient) or too small (which would create a bottleneck). We at Zhengzhou Keda offer a range of Solvent Recovery Machines because every lab and factory has different needs. From smaller research labs to large-scale industrial applications that might need continuous operation models, getting the capacity right is the first step to satisfaction. I usually ask, "How many liters of waste solvent do you need to process per day or week?" That gives us a good starting point.
Solvent Compatibility and Recovery Efficiency
Not all machines can handle all types of solvents. You must ensure the machine is built with materials compatible with the solvents you use. Some solvents are corrosive, others are very flammable, and they have different boiling points. The machine's seals, tank, and condenser must be able to withstand your specific chemicals. Also, ask about the expected recovery rate. A good machine should recover a high percentage of the pure solvent, typically over 90% or 95%. Our 16 years of experience in manufacturing laboratory and industrial equipment, including reactors and distillation systems, means we pay close attention to material science. We can help you choose a machine with the right materials of construction, like stainless steel of various grades, and ensure it is designed to maximize recovery for your specific solvents.
Safety and Automation Features
Safety is the most important thing. Look for machines with built-in safety features. These include things like over-temperature protection (to prevent overheating), pressure relief valves, and systems to prevent leaks. If you work with highly flammable solvents, you might need an explosion-proof model, designed to operate safely in such environments. Automation also contributes to safety and ease of use. Features like automatic shutdown when the cycle is complete, programmable settings for different solvents, and clear, user-friendly controls make the machine easier and safer to operate. As a CE and ISO9001 certified manufacturer, all our equipment, including solvent recovery machines, is designed with safety as a top priority. We include comprehensive safety interlocks and provide detailed operational guides.
Don't Forget After-Sales Support
Finally, consider the support you will get from the supplier after you buy the machine. What is the warranty period? Are spare parts readily available? Can you get technical assistance if you have questions or run into issues? A reliable supplier stands behind their products. My company, Zhengzhou Keda, was actually the first manufacturer in China to establish a 24/7 after-sales support team for laboratory instruments. We know that when you invest in important equipment like a solvent recovery machine, ongoing support provides peace of mind. We offer a one-year warranty, lifetime cost-price service for parts and maintenance, and our engineers, many of whom are fluent in English, are always ready to help. This commitment to service is a core part of our promise to our global customers.
Conclusion
Choosing a solvent recovery machine is a smart move for cost, safety, and our earth. It puts you in control of your solvent use, effectively.