Struggling with high solvent costs in your cannabis extraction? Worried about environmental impact and operational inefficiencies? It's a common headache for many processors looking to scale up.
Solvent recovery systems offer a powerful solution. They help you reclaim and reuse valuable solvents, drastically cutting operational expenses, improving safety, and promoting sustainable practices in your cannabis extraction facility.
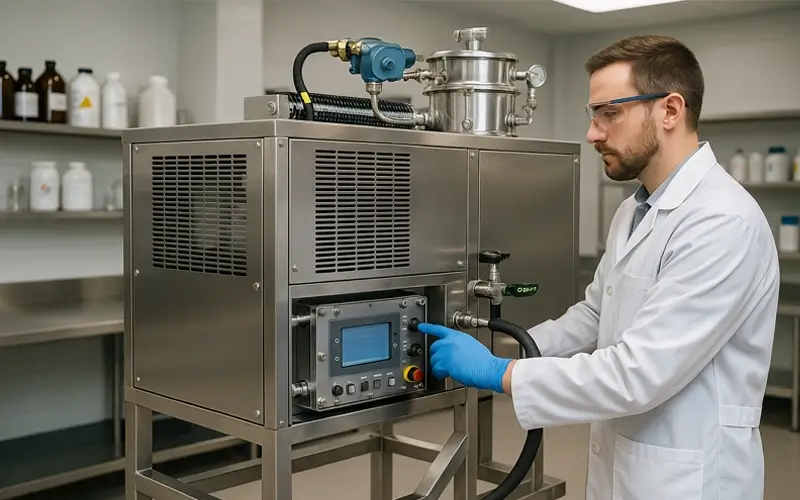
As someone who's been involved in the laboratory instrument field for over 16 years, I've seen firsthand how quickly the cannabis industry is evolving. Processors are constantly seeking ways to refine their methods, boost their bottom line, and meet increasingly stringent regulations. If you're not looking at solvent recovery, you might be missing out on significant advantages. Let's explore how this technology can be a game-changer for your operations. It's about more than just saving a bit of money; it's about smarter, cleaner, and more profitable processing.
What Exactly is Solvent Recovery and Why is it a Game-Changer for Cannabis Processors?
Feeling the pinch of recurring solvent purchases? Wondering if there's a more sustainable and cost-effective way to manage your extraction process without compromising quality?
Solvent recovery is the process of separating and reclaiming solvents from your extracted material and waste streams. For cannabis processors, it's a game-changer because it dramatically reduces solvent costs, minimizes environmental waste, and enhances overall lab safety and efficiency.
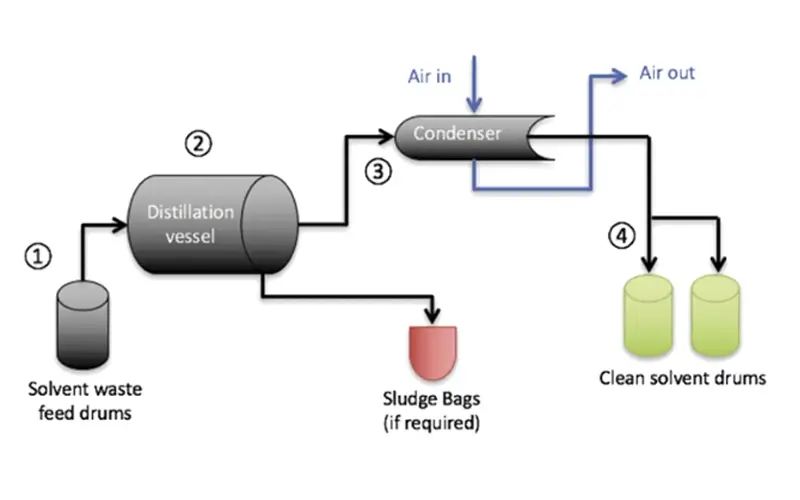
Think about how much solvent, like ethanol, you use in a single extraction run. Now, imagine being able to get back 90% or even more of that solvent to use again. That's what solvent recovery does. I've worked with many labs, and the ones that adopt effective solvent recovery see an almost immediate impact on their operational budget. It's not just a piece of equipment; it's a strategic investment.
The Core Principle: Separation and Reuse
At its heart, solvent recovery relies on the different boiling points of your solvent and your desired cannabis compounds (cannabinoids, terpenes). The mixture is heated, the solvent evaporates, and then it's condensed back into a liquid form, separate from your extract. This reclaimed solvent is often pure enough to be used directly in subsequent extractions. My experience shows that modern systems achieve very high purity levels for the recovered solvent. This capability means you're not just saving money but also maintaining the quality of your starting materials for the next batch.
Why it's More Than Just Cost Savings
While reducing the expenditure on solvents like ethanol or hydrocarbons is a primary driver, the benefits extend further. Implementing robust solvent recovery elevates the professionalism of your operation. It demonstrates a commitment to sustainable practices, which is increasingly important to consumers and regulators. It also contributes to a safer working environment by reducing the amount of solvent vapors and liquid solvent waste that needs handling and disposal. It transforms your facility into a more efficient, responsible, and ultimately more profitable business. From my perspective, it's a foundational technology for any serious cannabis processor today.
How Do Solvent Recovery Systems Actually Work to Save You Money?
Curious about the magic behind reclaiming solvents? Does the process seem too complex or expensive to implement, making you hesitant to explore its financial benefits?
Solvent recovery systems typically use evaporation and condensation. The solvent-laden mixture is heated, turning the solvent into vapor, which is then cooled and condensed back into a liquid, ready for reuse. This directly saves money by drastically reducing new solvent purchases.
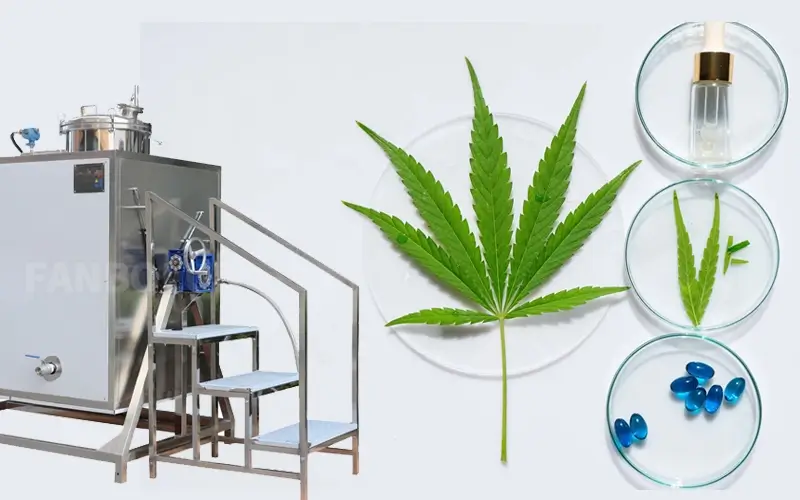
I often explain to clients that solvent recovery isn't black magic; it's based on solid scientific principles that we've utilized in labs for decades, now optimized for the cannabis industry. The process might sound technical, but modern systems are designed for ease of use. Let's break down the typical steps and components.
Key Stages in the Recovery Process:
Heating: The solution containing your solvent and extracted cannabis oil (often called a miscella) is gently heated. This is usually done in a controlled environment, like a rotary evaporator's heated bath or a falling film evaporator's heated tubes. The goal is to reach the solvent's boiling point without degrading the valuable cannabinoids and terpenes.
Evaporation: As the solvent reaches its boiling point, it turns into a vapor. This vapor still contains just the solvent, leaving the heavier cannabis oil behind. Creating a vacuum can lower the solvent's boiling point, making the process more efficient and gentler on the extract.
Condensation: The solvent vapor is then directed through a chilled condenser. As the vapor cools, it turns back into a liquid. This liquid is your recovered solvent. I always emphasize the importance of efficient cooling here – it directly impacts your recovery rates.
Collection: The condensed, purified solvent is collected in a separate receiving flask or tank, ready to be used again in your extraction process.
The direct financial saving comes from not having to buy new drums of solvent nearly as often. If you recover, say, 95% of your ethanol from each run, your solvent purchasing budget can shrink by a similar percentage. I've seen facilities recoup their investment in a solvent recovery system surprisingly quickly, sometimes within months, just from these savings alone. It's one of the most straightforward ROIs in cannabis processing equipment.
What are the Tangible Benefits of Investing in Solvent Recovery Beyond Just Cost Savings?
Thinking solvent recovery is only about cutting costs? Are you overlooking other crucial advantages that could significantly enhance your cannabis processing operations and brand reputation?
Beyond cost savings, solvent recovery offers enhanced product purity by removing residual solvents, improved workplace safety by minimizing solvent vapors, and strong environmental stewardship by reducing waste and emissions. It also boosts overall operational efficiency.
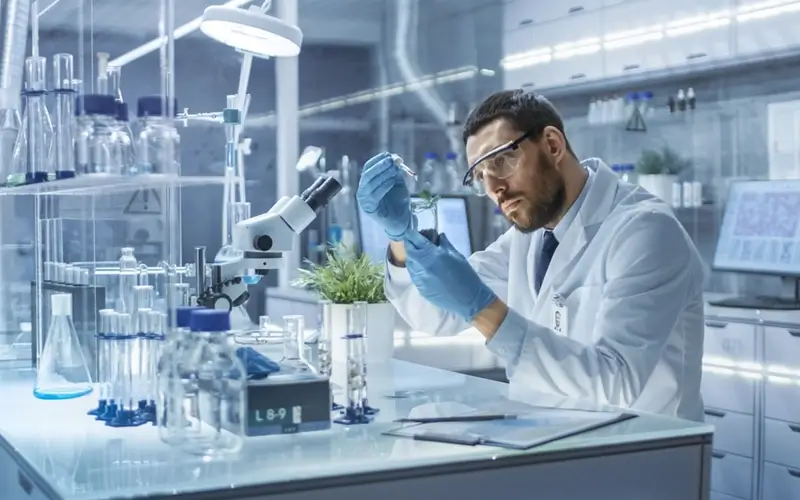
It's true, the financial argument for solvent recovery is compelling. I've helped many businesses calculate these savings, and they are substantial. However, focusing solely on cost reduction would mean missing a larger picture of operational excellence and responsibility. Let's explore these equally important benefits.
Enhanced Product Purity and Quality
One of the critical aspects of producing high-quality cannabis extracts is ensuring minimal residual solvent in the final product. Effective Thinner Recycler Machine are excellent at stripping solvents down to very low levels (PPMs). This not only meets regulatory requirements but also results in a cleaner, purer, and often better-tasting product. Customers appreciate this. In my experience, brands that can confidently state their products are free from residual solvents gain a competitive edge.
Improved Workplace Safety
Working with large volumes of flammable solvents inherently carries risks. By recovering and containing solvents within a closed-loop system, you significantly reduce the presence of solvent vapors in the lab environment. This minimizes fire and explosion hazards and reduces operator exposure to potentially harmful fumes. A safer lab is a more productive lab, and it’s something I always stress when discussing equipment choices. It's about protecting your most valuable asset: your team.
Environmental Responsibility
The cannabis industry, like any other, has an environmental footprint. Reducing solvent emissions into the atmosphere and minimizing hazardous waste are key aspects of sustainable operation. Solvent recovery is a green technology. By recycling solvents, you decrease the demand for new solvent production (which is energy-intensive) and reduce the amount of solvent waste that needs to be disposed of, often through costly hazardous waste services. This resonates well with environmentally conscious consumers and can be a strong part of your brand's story.
Increased Throughput and Efficiency
While it might seem like an extra step, integrating solvent recovery can actually streamline your overall workflow. By ensuring a consistent supply of clean, readily available solvent, you avoid bottlenecks caused by solvent shortages or the delays associated with frequent reordering and handling of new solvent drums. Efficient recovery can keep pace with your extraction, allowing for more continuous operations. I've seen labs increase their daily processing capacity simply by optimizing their solvent management through recovery.
Benefit Category | Specific Advantage | Impact on Your Business |
---|---|---|
Economic | Reduced solvent purchases | Higher profit margins, faster ROI |
Product Quality | Lower residual solvents | Safer products, better taste/aroma, premium branding |
Safety | Reduced solvent vapors & handling | Lower risk of accidents, improved employee health |
Environmental | Less waste, fewer emissions | Greener operations, better public image, compliance |
Operational | Consistent solvent supply | Smoother workflow, potential for higher throughput |
Which Solvents Commonly Used in Cannabis Extraction Can Be Effectively Recovered?
Unsure if the specific solvents you use for cannabis extraction are suitable for recovery? Worried that the recovery process might be too inefficient for your chosen solvent type?
Most common cannabis extraction solvents like ethanol, isopropyl alcohol (IPA), butane, propane, and hexane can be effectively recovered. Modern recovery systems are designed to handle these solvents efficiently, often achieving high recovery rates.
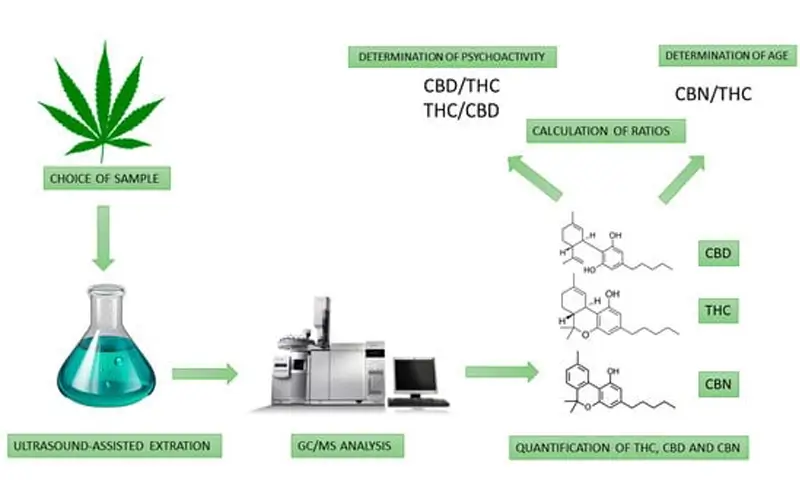
The versatility of solvent recovery equipment is a major plus. As a manufacturer, we design systems to be compatible with the solvents most frequently used in the botanical extraction space, especially cannabis. It's a question I get often: "Will your system work with my solvent?" The answer is usually a resounding yes, but there are nuances.
Ethanol: The Workhorse
Ethanol is arguably the most popular solvent in cannabis extraction due to its safety profile, effectiveness, and regulatory acceptance. I can tell you that ethanol recovery is highly efficient, with good quality systems often reclaiming 90-98% of the solvent. Because it's used in large volumes for biomass washing, efficient ethanol recovery is critical for profitability. We've focused heavily on optimizing our equipment for ethanol, ensuring high recovery rates and purity of the reclaimed solvent.
Hydrocarbons: Butane and Propane
Butane (n-butane, isobutane) and propane are favored for their ability to extract a specific profile of terpenes and cannabinoids, leading to products like BHO (Butane Hash Oil). Recovering these low-boiling-point hydrocarbons is standard practice and essential for safety and cost. These systems are typically closed-loop and designed to handle the pressures associated with these solvents. My colleagues specializing in hydrocarbon extraction systems always emphasize the integrated nature of recovery in these setups; it's not really optional.
Other Solvents: IPA, Hexane, Heptane
Isopropyl alcohol (IPA) is sometimes used as an alternative to ethanol. It can also be recovered efficiently, similar to ethanol, though its slightly different properties (e.g., azeotrope with water) are considered in system design. Hexane and heptane are less common for direct consumer products but might be used in certain refining steps or for specific extractions. These can also be recovered, though careful attention to their specific boiling points and safety handling procedures is needed. Generally, any solvent with a boiling point distinct from your target compounds can be recovered. The key is matching the equipment's capabilities (temperature range, vacuum depth, material compatibility) to the solvent's properties.
It's always good practice to discuss your specific solvent blend with the equipment manufacturer. We can provide guidance on expected recovery rates and any operational adjustments needed for optimal performance. My 16 years in this business have taught me that a little consultation upfront can save a lot of headaches later.
What Key Features Should You Prioritize When Selecting a Solvent Recovery System for Your Lab?
Overwhelmed by the options for solvent recovery systems? Unsure which features truly matter for safety, efficiency, and long-term reliability in your cannabis operations?
Prioritize high recovery rates, appropriate capacity for your scale, robust safety features (like over-temp protection, certified components), ease of use, durable materials, and reliable manufacturer support when selecting a solvent recovery system.
Solvent Recycling Equipment (90L)
Model: T-90EX
Feed capacity(L): 90
Power(kW): 5
Recovery(%): 95
View MoreSolvent Recycler Machine (125L)
Model: T-125EX
Feed capacity(L): 125
Power(kW): 6
Recovery(%): 95
View MoreSolvent Recycling Machine (250L)
Model: T-250EX
Feed capacity(L): 250
Power(kW): 16
Recovery(%): 95
View MoreSolvent Recycling System (600L)
Model: T-600EX
Feed capacity(L): 600
Power(kW): 32
Recovery(%): 95
View More
Choosing the right solvent recovery system is a critical decision. It's not just about the initial price; it's about the long-term value, reliability, and safety it brings to your lab. Based on my experience helping countless clients, here's what I advise them to look for:
1. Recovery Rate and Efficiency
This is paramount. A system that recovers 95% of your solvent is significantly better than one that only manages 85%. Ask for documented recovery rates for your specific solvent. Higher efficiency means faster payback and lower ongoing costs. This often ties into the quality of the condenser, the vacuum system, and the precision of temperature control. We constantly invest in R&D to maximize these rates in our equipment.
2. Capacity and Scalability
The system must match your current processing volume and ideally offer some room for growth. Consider batch sizes or continuous flow rates. A system that's too small will become a bottleneck. Conversely, an oversized system might be inefficient for smaller runs. I always advise clients to think about their one-year and three-year plans when sizing equipment.
3. Safety Features
This cannot be overstated, especially when dealing with flammable solvents. Look for:
Over-temperature protection.
Over-pressure protection (if applicable).
Spark-proof or explosion-proof components (especially for motors, heating elements, and control panels if operating in classified areas or with highly volatile solvents).
Leak detection or robust sealing technology.
Compliance with recognized safety standards (e.g., CE marking, UL listing for components). As a manufacturer with ISO9001 and CE certificates, we build these features in.
4. Ease of Use and Maintenance
Your team needs to operate and maintain the equipment efficiently. Intuitive controls, easy cleaning, and straightforward maintenance procedures will save time and reduce errors. I've seen overly complex systems gather dust because operators found them too cumbersome. Look for clear manuals and accessible parts.
5. Material Compatibility and Durability
The materials in contact with your solvents and extracts (glassware, seals, tubing) must be resistant to corrosion and degradation. High-quality borosilicate glass and appropriate gasket materials (like PTFE) are essential for longevity and product purity. The overall build quality should be robust for daily lab use. Durability is a hallmark of "International Quality" that we strive for.
6. Manufacturer Reliability and Support
Choose a reputable manufacturer with a proven track record. What kind of warranty is offered? Is technical support readily available? Can they provide spare parts quickly? Our 16 years of export experience and 24/7 after-sales support team are things we're proud of because we know how critical uptime is for our customers. Don't underestimate the value of good post-sales service.
How Can You Seamlessly Integrate Solvent Recovery into Your Current Extraction Workflow?
Worried that adding solvent recovery will complicate your existing setup? Concerned about the downtime or major changes required to integrate a new system effectively?
Seamless integration involves planning for space and utilities, ensuring compatibility with existing extraction machinery, adapting SOPs, and proper team training. With good planning and manufacturer support, it can be a smooth transition.
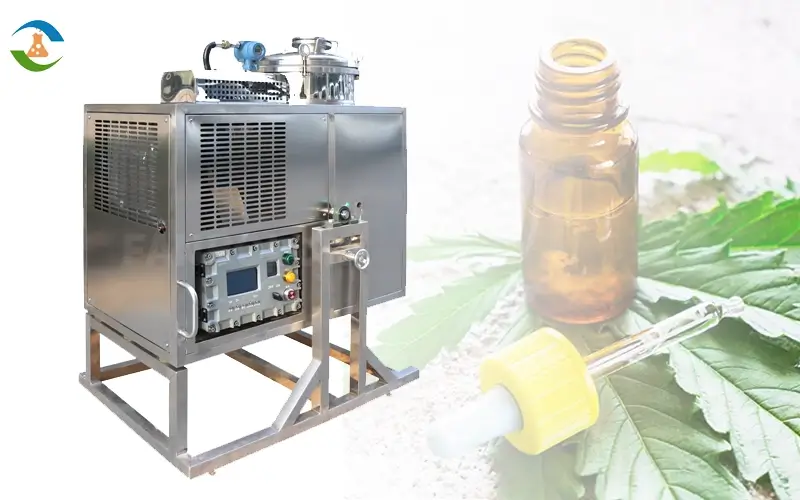
Integrating a new piece of major equipment like a solvent recovery system can seem daunting, but it doesn't have to be a major disruption. I've guided many facilities through this process. With thoughtful planning, it can be a surprisingly smooth transition that quickly starts paying dividends.
1. Planning for Space and Utilities
Before the equipment arrives, assess your lab space. Solvent recovery systems, especially larger ones, need adequate footprint. Consider vertical space too if you're looking at taller systems like some falling film evaporators. You'll also need to ensure you have the necessary utilities:
Power: Check voltage, phase, and amperage requirements. Dedicated circuits are often recommended.
Vacuum Source: Many recovery systems require a vacuum pump. Ensure yours is adequate or factor in a new one.
Cooling: Condensers need a cooling medium, typically a recirculating chiller. Match the chiller's capacity to the recovery system's needs for optimal performance.
Ventilation: While systems are generally closed, good lab ventilation is always important.
2. Ensuring Equipment Compatibility
Your solvent recovery unit needs to connect with your primary extraction equipment. For example, if you're using large-scale rotary evaporators for recovery after ethanol extraction, how will the solvent-laden ethanol be transferred? How will the recovered solvent be moved back to storage or for reuse? Think about transfer lines, pumps (if needed), and compatible fittings. We often discuss these interface points during the sales process to ensure a good fit.
3. Adapting Standard Operating Procedures (SOPs)
You'll need to develop or update your SOPs to include the operation of the solvent recovery system. This includes startup, operation, shutdown, cleaning, and routine maintenance. Clear SOPs are vital for consistent results and safe operation. I've found that involving the operating team in developing these SOPs can improve buy-in and adherence.
4. Team Training and Support
Proper training for your staff is crucial. They need to understand how the system works, how to operate it safely, and how to perform basic troubleshooting. This is where a good manufacturer plays a key role. We offer training and comprehensive manuals. And our "24/7 after-sales support" means we're there if questions or issues arise after installation. Never underestimate the value of a well-trained team; they are key to maximizing the benefits of your new equipment.
By considering these factors, you can make the integration of solvent recovery a value-adding step, not a complicated hurdle. My aim is always to help clients achieve not just an installation, but a successful operational enhancement.
Conclusion
Investing in solvent recovery is a smart move for serious cannabis processors. It cuts costs, boosts safety, protects the environment, and ultimately, improves your bottom line effectively.