Are you struggling with methyl ethyl ketone (MEK) waste? It's a common headache, costly and tricky to handle right. You want a solution that's safe and smart.
Responsible MEK waste disposal involves understanding regulations, minimizing waste generation, and exploring recycling options. For many businesses like yours, using a solvent recovery system can be a highly effective and economical approach to manage MEK waste safely and sustainably.
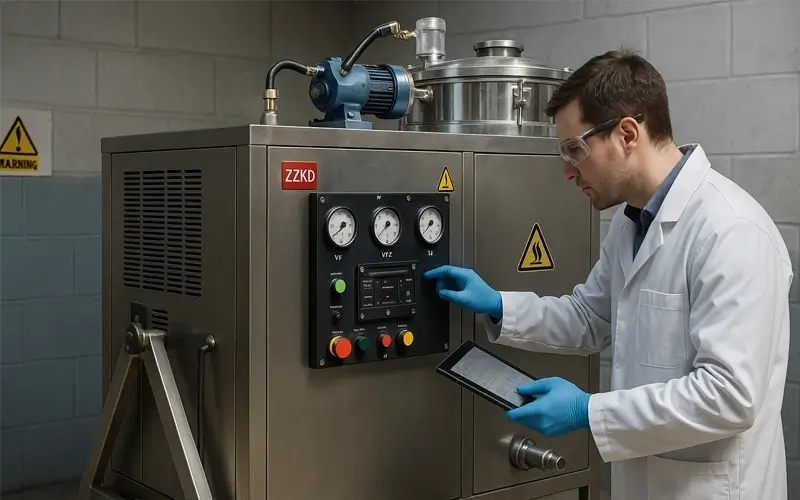
As a company that has specialized in laboratory and industrial equipment for over 16 years, we've talked to many businesses. We understand the challenges you face. MEK is a powerful solvent, essential in many industries. But its disposal can be a real puzzle. You need to protect your workers, the environment, and your bottom line. Let's explore how to tackle this. We believe there are better ways than just paying for disposal.
What Makes Disposing of MEK Waste So Challenging?
Is MEK waste giving you sleepless nights? Its flammable nature and strict rules make disposal a complex and often expensive task for many companies.
Disposing of MEK waste is challenging due to its hazardous properties, including flammability and toxicity. Strict environmental regulations govern its handling and disposal, requiring specialized procedures and often leading to high costs for businesses trying to comply.

From our experience helping customers worldwide, the main difficulties with MEK waste really boil down to a few key areas. First, MEK is classified as a hazardous waste. This isn't just a label; it means specific, often costly, handling and disposal methods are mandatory. You can't just pour it down the drain or send it to a regular landfill. I remember one client who, before working with us, faced hefty fines for improper storage – a simple mistake that cost them dearly.
Key Challenges in MEK Disposal:
Regulatory Hurdles: Environmental agencies have tight rules. These rules cover everything from how you store the waste on-site to how it's transported and finally processed. Keeping up with these regulations can feel like a full-time job.
Safety Risks: MEK is highly flammable. This poses a significant fire risk if not handled correctly. There are also health risks for employees exposed to its fumes. Ensuring proper ventilation and personal protective equipment is vital.
High Disposal Costs: Because it's hazardous, specialized waste management companies must handle MEK. Their services are not cheap. These costs can add up quickly, especially for businesses that generate a lot of MEK waste. We've seen disposal bills that significantly impact a company's profitability.
Environmental Impact: If MEK isn't disposed of correctly, it can contaminate soil and water. This is a big concern for environmentally conscious companies and for meeting community expectations. The long-term liability for environmental damage can be enormous.
These challenges mean that just "getting rid of" MEK waste isn't a simple task. It requires careful planning and a responsible approach. Many businesses we talk to are actively looking for ways to reduce these burdens.
Are There Cost-Effective Ways to Manage MEK Waste?
Worried about the mounting bills for MEK waste disposal? You're not alone. Many businesses are searching for smarter ways to manage these expenses without cutting corners on safety.
Yes, cost-effective MEK waste management is achievable. Key strategies include minimizing initial MEK use, segregating waste streams properly, and investing in on-site solvent recovery systems to recycle and reuse MEK, drastically reducing disposal volumes and costs.
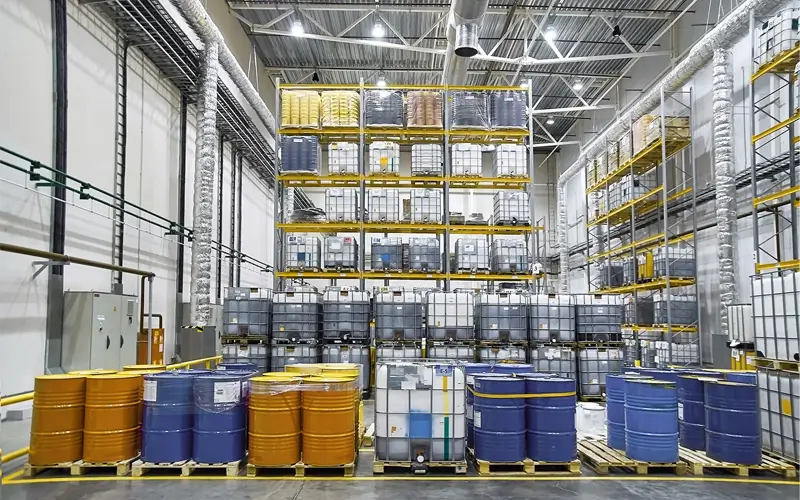
We've seen firsthand how businesses can significantly cut costs associated with MEK waste. It’s not just about finding the cheapest disposal service; it's about a more holistic approach. One of the most impactful strategies we recommend is on-site solvent recovery. Think about it: instead of paying someone to take away your used MEK, what if you could clean it and reuse it?
Strategies for Cost Reduction:
Waste Minimization at the Source: This is the first step. Can you optimize your processes to use less MEK? Sometimes, simple changes in application methods or equipment cleaning procedures can make a big difference. We once worked with a printing company that, through minor adjustments we suggested for their cleaning process, reduced their MEK consumption by 15%.
Proper Waste Segregation: Don't mix MEK waste with other, less hazardous wastes. Contaminated MEK is often more expensive to dispose of. Keeping waste streams separate can lower overall disposal costs.
Exploring On-Site Recycling: This is where a Solvent Recovery System comes into play. These systems distill the used MEK, separating it from contaminants. The recovered MEK can often be reused in your processes, sometimes multiple times. This directly reduces the amount of new MEK you need to buy and the amount of waste you need to pay to dispose of. The return on investment can be surprisingly quick. For example, a client in the automotive parts manufacturing sector found that their solvent recovery unit paid for itself in just under 18 months through savings on new solvent purchases and disposal fees.
Strategy | Potential Cost Impact | Implementation Notes |
---|---|---|
Waste Minimization | Moderate Savings | Process review, employee training |
Waste Segregation | Small to Moderate Savings | Clear labeling, dedicated containers |
On-Site Solvent Recovery | Significant Long-Term Savings | Initial investment in equipment, operational procedure adjustments |
It’s about shifting from a "dispose-at-all-costs" mindset to a "recover-and-reuse" strategy. This not only saves money but also enhances your company's environmental credentials. We believe this is the future of responsible solvent management.
Can Recycling MEK Actually Benefit My Business?
Thinking about MEK recycling but unsure if it's worth it? Many businesses wonder if the effort translates into real, tangible benefits beyond just being "green."
Absolutely. Recycling MEK using a solvent recovery system offers significant business benefits. These include drastic reductions in waste disposal costs, lower expenditure on new solvent purchases, and an improved environmental profile, enhancing your brand's reputation.
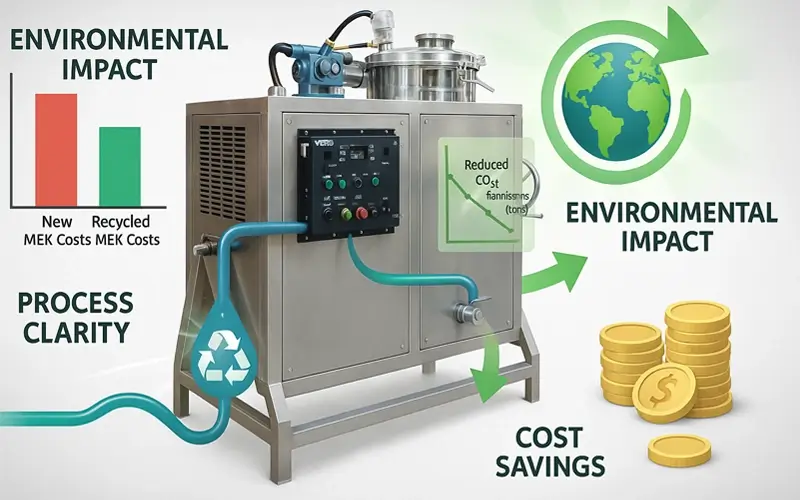
As manufacturers of Solvent Recovery Systems, we've seen the transformative impact of MEK recycling on many businesses. The benefits go far beyond just meeting environmental regulations. It's a smart business move. I recall a conversation with a customer who initially hesitated due to the upfront cost of a recovery unit. A year later, they called to tell us it was one of the best investments they'd made.
Tangible Benefits of MEK Recycling:
Drastic Cost Savings: This is usually the biggest driver.
Reduced Disposal Fees: The less waste you send out, the less you pay. Some of our clients have cut their hazardous waste disposal volumes by over 90%.
Lower New Solvent Purchases: Reusing your MEK means buying less virgin solvent. With fluctuating solvent prices, this creates budget stability. Imagine cutting your new MEK purchases by 50-80% or even more.
Environmental Responsibility: Recycling MEK demonstrates a commitment to sustainability. This can enhance your company's image with customers, stakeholders, and the community. It’s a powerful message, especially as consumers and partners increasingly value eco-friendly practices. We have helped companies achieve ISO 14001 certification partly through implementing solvent recycling.
Operational Efficiency: Having a ready supply of recycled MEK on-site can reduce reliance on external suppliers and protect against potential supply chain disruptions. This ensures smoother, more predictable operations.
Improved Safety: By handling less volume of new solvents and waste, you can reduce the risks associated with transportation and storage of hazardous materials.
Consider this: every liter of MEK you recycle is a liter you don't pay to dispose of and a liter you don't have to buy new. The cumulative effect on your finances and environmental footprint can be substantial. We've seen companies turn a significant operational cost into a source of savings and a point of pride. It's about creating a closed-loop system within your own facility.
What Should I Consider When Choosing an MEK Recovery Method?
Ready to explore MEK recovery, but unsure what to look for? Selecting the right method or system is key to maximizing benefits and ensuring smooth operation.
When choosing an MEK recovery method, consider the volume and contamination level of your waste, required purity of recovered MEK, safety features of the equipment, ease of operation and maintenance, and the supplier's after-sales support. An on-site distillation-based solvent recovery system is often ideal.
Solvent Recycling Equipment (90L)
Model: T-90EX
Feed capacity(L): 90
Power(kW): 5
Recovery(%): 95
View MoreSolvent Recycler Machine (125L)
Model: T-125EX
Feed capacity(L): 125
Power(kW): 6
Recovery(%): 95
View MoreSolvent Recycling Machine (250L)
Model: T-250EX
Feed capacity(L): 250
Power(kW): 16
Recovery(%): 95
View MoreSolvent Recycling System (600L)
Model: T-600EX
Feed capacity(L): 600
Power(kW): 32
Recovery(%): 95
View More
Choosing the right MEK recovery solution is crucial. As a company that has specialized in this equipment for over 16 years, we advise customers to think carefully about their specific needs. It's not a one-size-fits-all situation. We once had a client purchase a system too small for their actual waste volume, which led to bottlenecks. Proper assessment upfront is key.
Key Considerations for Your MEK Recovery System:
Capacity and Throughput: How much MEK waste do you generate per day or week? The system should be able_ to handle your typical volume, with some capacity for growth.
Purity Requirements: What level of purity do you need for the recovered MEK to be reused in your processes? Different systems offer different purification efficiencies. Simple distillation is common for MEK.
Types of Contaminants: What is mixed with your MEK? Resins, pigments, oils, water? The nature of contaminants will influence the type of recovery system (e.g., simple distillation, fractional distillation) and its effectiveness. Our systems are designed to handle a wide range of common contaminants.
Automation and Ease of Use: Modern systems offer varying degrees of automation. Consider how much operator involvement is acceptable. Look for user-friendly controls and clear operating procedures. We prioritize ease of use in our designs.
Safety Features: Since MEK is flammable, safety is paramount. Ensure the system has features like explosion-proof construction (where necessary), over-temperature protection, and pressure relief valves. Our equipment is CE certified, meeting stringent safety standards.
Footprint and Installation: Do you have enough space for the equipment? What are the utility requirements (electricity, cooling water)?
Maintenance and Support: What are the routine maintenance requirements? Does the supplier offer reliable technical support and spare parts availability? We pride ourselves on our 24/7 after-sales support and global reach.
Cost-Benefit Analysis: Evaluate the total cost of ownership (initial investment, operating costs, maintenance) against the projected savings from reduced disposal and new solvent purchases. The payback period is an important metric.
We always encourage potential customers to discuss their specific waste stream and operational needs with us. As an experienced manufacturer, we can help guide you to the most suitable Solvent Recovery System, ensuring it’s a valuable asset for your business for years to come. A factory visit or a detailed technical exchange can often clarify the best path forward.
Effectively managing MEK waste through recovery is smart, sustainable, and saves money. We're here to help you find the right solution.