Disposing of paint thinner can be a daunting task, especially considering the environmental hazards and legal restrictions surrounding its disposal. Paint thinners, including mineral spirits, acetone, and other solvents, are essential in the painting industry for thinning oil-based paints and cleaning brushes and equipment. However, once used, they become contaminated with paint particles and other residues, turning them into hazardous waste. The improper disposal of paint thinner can lead to severe environmental damage, including soil and water contamination, and poses a threat to human health. So, how can one dispose of paint thinner in an environmentally responsible manner?
Understanding the Importance of Proper Disposal
Paint thinner is typically made from organic solvents like mineral spirits, acetone, or turpentine. These substances are flammable and can be toxic to humans, animals, and the environment. Improper disposal can lead to soil and water contamination, posing significant health risks. Paint thinners are classified as hazardous waste by the Environmental Protection Agency (EPA) due to their flammability and toxicity. When improperly disposed of, these chemicals can seep into the ground, polluting soil and groundwater. This contamination not only harms wildlife but also poses a risk to human health, as these toxic substances can make their way into drinking water supplies.
Moreover, improper disposal can result in hefty fines and legal repercussions for businesses. Regulatory bodies have strict guidelines for the disposal of hazardous waste, and non-compliance can lead to significant financial penalties. Therefore, it is not just an environmental issue but also a legal and financial concern for companies.
Steps for Disposing of Paint Thinner
STEP 1: Strain, Seal, and Save for Reuse
Allow used paint thinner to sit in a sealed container. The paint residue will settle at the bottom, leaving the clear thinner on top. Carefully pour off the clear liquid into another container for future use. Ensure the container is tightly sealed and labeled.
Important Note: Make sure the container is clearly labeled to avoid accidental misuse. Store it in a cool, dry place away from heat sources and out of reach of children and pets.
STEP 2: Dispose of Empty Containers with Household Trash
Once a paint thinner container is completely empty, it can be discarded with your regular household trash. Make sure the container is fully dry and does not contain any liquid residue before disposal.
Important Note: Confirm that the container is completely empty and dry to prevent any risk of fire or contamination in the trash.
STEP 3: Take Leftover Paint Thinner to a Hazardous Waste Facility
For any leftover paint thinner that cannot be reused, take it to a local hazardous waste disposal facility. Many communities have designated days or locations for collecting hazardous materials.
Important Note: Transport the paint thinner in a sealed, labeled container. Do not mix it with other types of waste. Follow the facility’s guidelines for drop-off procedures.
STEP 4: Properly Dispose of Soaked Rags at a Hazardous Waste Facility
Household or shop rags soaked with paint thinner should also be taken to a hazardous waste facility. Do not throw them in the regular trash as they are flammable and pose a fire hazard.
Important Note: Store soaked rags in a sealed, fireproof container until you can take them to the hazardous waste facility. Keep them away from other combustible materials and heat sources.
Tools and Materials Needed
Sealed Containers:
For storing and disposing of paint thinner.
Absorbent Material:
Such as cat litter or sawdust, for solidifying small amounts of paint thinner.
Protective Gear:
Including gloves, safety glasses, and a mask to protect yourself from fumes and contact.
Plastic Bags:
For disposing of solidified paint thinner.
Traditional Methods of Disposal: Are They Enough?
Traditionally, the disposal of paint thinner involved either taking it to a hazardous waste disposal facility or letting the thinner evaporate in a well-ventilated area before disposing of the residue. While these methods are still commonly used, they are far from ideal.
Taking paint thinner to a hazardous waste facility ensures that it is disposed of according to legal guidelines, but it is not a sustainable solution. The chemicals still end up as waste, and the process involves transportation, which adds to the carbon footprint.
Evaporation, on the other hand, is a risky and environmentally harmful method. Allowing paint thinner to evaporate releases volatile organic compounds (VOCs) into the atmosphere, contributing to air pollution and posing health risks to anyone nearby.
These traditional methods may seem convenient, but they do not address the root problem—waste generation. Is there a more sustainable and cost-effective solution?
The Role of Solvent Recovery Machines
This is where solvent recovery machines come into play. These machines are designed to recycle used solvents, including paint thinners, by separating the contaminants from the solvent. The result is a clean, reusable solvent that can be used in future projects, significantly reducing the amount of hazardous waste generated.
How Do Solvent Recovery Machines Work?
Solvent recovery machines operate on a relatively simple principle—distillation. The contaminated solvent is heated in a closed system, causing it to evaporate. The vapor is then condensed back into liquid form, leaving behind the impurities, which can be safely disposed of. The recovered solvent is now clean and can be reused for thinning paint or cleaning equipment.
The process is efficient and effective, often recovering up to 95% of the solvent. This not only reduces the need to purchase new solvents but also minimizes the volume of hazardous waste that needs to be disposed of.
Benefits of Using Solvent Recovery Machines
Environmental Benefits: One of the most significant advantages of using solvent recovery machines is the reduction in hazardous waste. By recycling paint thinner, businesses can significantly decrease their environmental impact. Fewer toxins are released into the environment, and the carbon footprint associated with producing and transporting new solvents is reduced.
Cost Savings: While the initial investment in a solvent recovery machine may seem substantial, the long-term cost savings are undeniable. By reusing solvents, businesses can reduce their purchasing costs. Additionally, the reduction in hazardous waste disposal fees and potential legal fines adds to the financial benefits.
Compliance with Regulations: As mentioned earlier, improper disposal of paint thinner can lead to legal issues. Solvent recovery machines help businesses comply with environmental regulations by reducing the volume of hazardous waste and ensuring that any waste generated is properly managed.
Improved Workplace Safety: Storing large quantities of used paint thinner poses a fire hazard. By recycling the solvent, businesses can reduce the amount of hazardous material on-site, thereby improving overall workplace safety.
Sustainability: In today’s world, sustainability is not just a buzzword but a necessity. Businesses are increasingly being held accountable for their environmental impact. Implementing solvent recovery not only enhances a company’s sustainability efforts but also improves its public image.
Is Investing in a Solvent Recovery Machine Worth It?
At this point, you might be wondering if investing in a solvent recovery machine is worth the cost. This is a valid question, especially for smaller businesses or those just starting out. The answer largely depends on the volume of paint thinner used and the long-term goals of the business.
“For companies that use large quantities of solvents, the return on investment can be substantial. The savings on purchasing new solvents and the reduction in disposal costs can quickly offset the initial investment. Moreover, as environmental regulations become stricter, having a solvent recovery system in place could protect businesses from future legal and financial liabilities.”
On the other hand, for smaller businesses or those with limited solvent use, it might seem like a significant expense. However, even in these cases, the long-term benefits of sustainability and regulatory compliance should not be overlooked. Additionally, as more businesses adopt solvent recovery technologies, the cost of these machines is likely to decrease, making them more accessible to a broader range of companies.
How to Choose a Solvent Recovery Machine?
Type of recovered solvent: clarify the type of solvent to be recovered. Different solvent recovery machines may be optimized for different solvents. Make sure the selected equipment can effectively recover the solvents you need.
Recovery efficiency and processing capacity: determine the required recovery efficiency and processing capacity. Large production lines require equipment with high recovery rates and large processing volumes, while small laboratories may pay more attention to the flexibility and precision of the equipment.
Safety: whether the equipment has explosion-proof design, multiple safety protection mechanisms (such as temperature protection, pressure protection, etc.) and certification in accordance with relevant safety standards (such as CE, UL, etc.).
Convenience of operation: choose equipment that is easy to operate and maintain. Consider whether the control interface of the equipment is intuitive, whether it supports Chinese display, whether it has remote monitoring function, etc.
Energy consumption and cost: equipment with high energy efficiency ratio and good energy saving effect can reduce long-term operating costs.
After-sales service: support in equipment installation and commissioning, technical training, troubleshooting and accessories supply.
Brand and reputation: choose well-known brands and suppliers with good reputation. A more complete product line and a wider user group can provide more reliable products and services.
Solvent Recycling Equipment (90L)
Model: T-90EX
Feed capacity(L): 90
Power(kW): 5
Recovery(%): 95
View MoreSolvent Recycler Machine (125L)
Model: T-125EX
Feed capacity(L): 125
Power(kW): 6
Recovery(%): 95
View MoreSolvent Recycling Machine (250L)
Model: T-250EX
Feed capacity(L): 250
Power(kW): 16
Recovery(%): 95
View MoreSolvent Recycling System (600L)
Model: T-600EX
Feed capacity(L): 600
Power(kW): 32
Recovery(%): 95
View More
How to Implement Solvent Recovery in Your Business
If you decide that a solvent recovery machine is the right choice for your business, the next step is to implement the system effectively. Here are some steps to consider:
Assess Your Needs: Begin by evaluating the volume of paint thinner your business uses and the amount of waste generated. This will help determine the size and capacity of the solvent recovery machine you need.
Choose the Right Machine: There are various types of solvent recovery machines available, each with different capacities and features. It is essential to choose a machine that fits your business’s specific needs. Consider factors such as the types of solvents used, the volume of waste generated, and the space available for the machine.
Train Your Staff: Proper training is crucial to ensure that the solvent recovery process is carried out effectively and safely. Employees should be trained on how to operate the machine, handle the recovered solvent, and manage the waste byproducts.
Monitor and Maintain: Like any equipment, solvent recovery machines require regular maintenance to ensure they operate efficiently. Establish a maintenance schedule and monitor the machine’s performance to maximize its lifespan and efficiency.
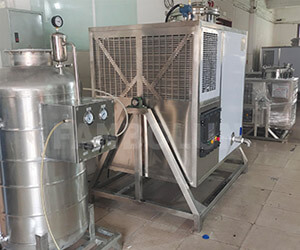
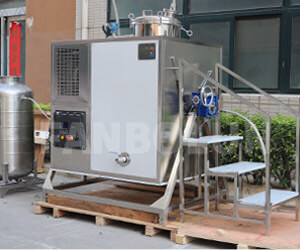
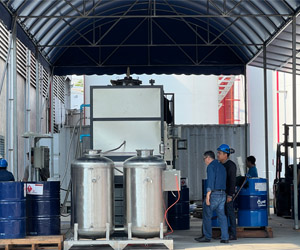
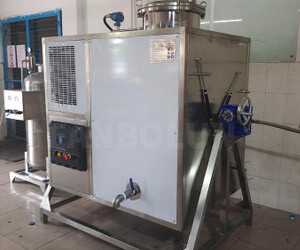
What About the Waste Left Behind?
You might be curious about what happens to the waste left behind after the solvent is recovered. This residue, often referred to as still bottoms, is the concentrated contaminants that were separated from the solvent during the distillation process. So, what should be done with this waste?
Still bottoms are classified as hazardous waste and must be disposed of according to local regulations. While the volume of this waste is significantly smaller than the original contaminated solvent, it still requires proper disposal. Some companies choose to have it incinerated, while others send it to a hazardous waste facility. It is crucial to follow all legal guidelines to ensure compliance and protect the environment.
Disposing of paint thinner is a challenge that requires careful consideration and responsible action. While traditional disposal methods are still in use, they fall short of providing a sustainable solution. Solvent recovery machines offer a viable alternative, allowing businesses to recycle paint thinner, reduce hazardous waste, and save on costs.
Investing in a solvent recovery system not only aligns with environmental and regulatory demands but also demonstrates a commitment to sustainability—a value increasingly recognized by consumers and business partners alike. As we move toward a more environmentally conscious future, the adoption of such technologies will play a crucial role in minimizing our impact on the planet. Are you ready to take the next step toward sustainable waste management?
By embracing solvent recovery, businesses can turn a waste problem into an opportunity for savings and sustainability. It’s a win-win for the environment and the bottom line.