If you work in industries like pharmaceuticals, textiles, printing, or automotive manufacturing, you’ve likely heard of caustic recovery or solvent recovery. But what exactly is the caustic recovery process? Why is it important for your business? And how can modern solvent recovery machines help you cut costs, reduce waste, and meet environmental regulations?
In this article, we’ll break down everything you need to know about the caustic recovery process in simple terms. By the end, you’ll understand how this technology works, why it matters for your operations, and how investing in a solvent recovery machine can transform your business.
1. What Is the Caustic Recovery Process?
Let’s start with the basics. The caustic recovery process (also called solvent recovery) is a method used to clean, recycle, and reuse industrial chemicals like solvents, caustic soda (sodium hydroxide), or acids. These chemicals are often used in manufacturing processes for cleaning, degreasing, coating, or dissolving materials.
For example:
A printing company uses solvents to clean ink from machinery.
A pharmaceutical factory uses caustic solutions to sterilize equipment.
An automotive plant uses degreasers to prepare metal parts for painting.
After these chemicals are used, they become contaminated with oils, dirt, or other waste. Instead of disposing of them as hazardous waste, the caustic recovery process purifies and recycles these chemicals, allowing businesses to reuse them multiple times.
2. Why Is Caustic Recovery Important?
Before diving into how it works, let’s address the “why.” Here are three key reasons businesses adopt solvent recovery systems:
A. Save Money on Chemical Costs
Fresh industrial solvents and caustic chemicals are expensive. Disposing of used chemicals is even costlier due to hazardous waste fees. By recycling solvents, companies reduce their need to buy new chemicals and cut disposal costs.
B. Meet Environmental Regulations
Governments worldwide are tightening rules around chemical disposal to protect air, water, and soil. Improper disposal can lead to fines or legal issues. A solvent recovery machine helps businesses stay compliant by minimizing waste.
C. Improve Sustainability
Recycling chemicals reduces your company’s environmental footprint. This aligns with global trends toward eco-friendly manufacturing and can enhance your brand’s reputation.
3. How Does the Caustic Recovery Process Work?
The exact steps vary depending on the type of solvent or chemical being recovered. However, most systems follow these general stages:
Step 1: Collection of Used Chemicals
Contaminated solvents or caustic solutions are collected from industrial processes. For example, dirty degreaser from a parts-cleaning tank.
Step 2: Filtration
The waste liquid is filtered to remove solid impurities like metal shavings, dust, or sludge.
Step 3: Distillation or Evaporation
This is the core of the recovery process. The filtered liquid is heated in a closed system. Since solvents and caustic chemicals have different boiling points, heating separates the pure chemical from contaminants.
Example: If recovering isopropyl alcohol (IPA), the machine heats the waste liquid to 82°C (IPA’s boiling point). The IPA evaporates, leaving behind oils or residues. The vapor is then cooled back into liquid form for reuse.
Step 4: Neutralization (For Caustic Solutions)
If recovering caustic soda or acids, the solution may need pH adjustment to restore its effectiveness.
Step 5: Reuse
The purified chemical is stored and reused in the same process, closing the loop.
4. What Are the Benefits of Using a Solvent Recovery Machine?
Investing in a solvent recovery system isn’t just about “going green.” It delivers measurable business advantages:
A. Cost Savings
Reduce chemical purchases by up to 90%.
Slash hazardous waste disposal costs.
Lower energy bills compared to traditional methods (modern machines are energy-efficient).
B. Increased Efficiency
Automated systems require minimal supervision.
Faster turnaround compared to outsourcing waste disposal.
C. Safety Improvements
Closed-loop systems reduce workers’ exposure to hazardous chemicals.
Compliance with OSHA and other safety standards.
D. Environmental Impact
Reduce landfill waste and groundwater pollution.
Lower carbon emissions by minimizing chemical production demand.
5. Key Features of a Modern Solvent Recovery Machine
Not all recovery systems are created equal. Here’s what to look for when choosing equipment:
A. Durability
Industrial solvents and caustic chemicals can be corrosive. Machines made of stainless steel or corrosion-resistant materials last longer.
B. Automation
Look for features like automatic temperature control, self-cleaning, and safety shutoffs.
C. Energy Efficiency
Systems with heat recovery technology reuse energy during distillation, cutting power costs.
D. Scalability
Choose a machine that matches your daily solvent usage. For example, small units handle 20 liters per batch, while large systems process 500+ liters.
E. Compliance Certifications
Ensure the machine meets international standards (CE, UL, ISO, etc.) for safety and environmental performance.
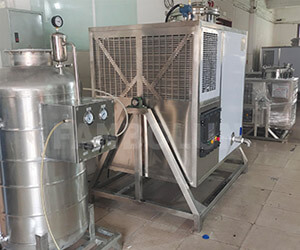
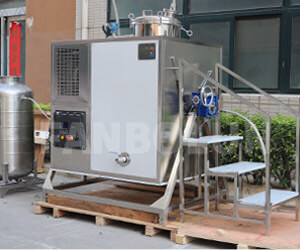
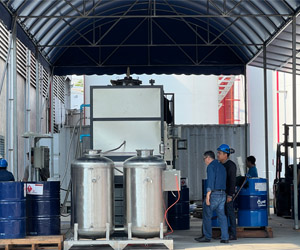
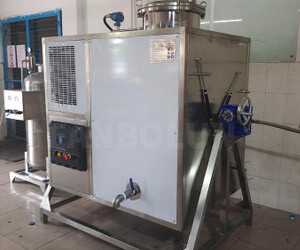
6. Common Questions About Solvent Recovery
Let’s answer some frequently asked questions:
Q1: How much money can I save with a solvent recovery machine?
Most businesses recover their investment in 6–18 months. For example, if you spend 10,000monthlyonsolvents,recyclingcouldsave10,000monthlyonsolvents,recyclingcouldsave8,000–$9,000 per month.
Q2: Is the process safe?
Yes, when using properly designed equipment. Modern machines include explosion-proof designs, leak detectors, and pressure relief valves.
Q3: Can all solvents be recovered?
Most common solvents (acetone, IPA, ethanol) and caustic solutions can be recycled. However, mixed chemicals or highly contaminated waste may require pre-treatment.
Q4: How do I maintain the machine?
Maintenance is simple: regular cleaning, replacing filters, and annual professional inspections.
7. Real-World Applications of Solvent Recovery Machines
Here’s how industries are benefiting:
Textile Manufacturing: Recover caustic soda used in fabric dyeing, saving $50,000+ annually.
Printing: Recycle ink solvents, reducing waste by 80%.
Electronics: Reuse degreasers for circuit board cleaning, improving workplace safety.
Solvent Recycling Equipment (90L)
Model: T-90EX
Feed capacity(L): 90
Power(kW): 5
Recovery(%): 95
View MoreSolvent Recycler Machine (125L)
Model: T-125EX
Feed capacity(L): 125
Power(kW): 6
Recovery(%): 95
View MoreSolvent Recycling Machine (250L)
Model: T-250EX
Feed capacity(L): 250
Power(kW): 16
Recovery(%): 95
View MoreSolvent Recycling System (600L)
Model: T-600EX
Feed capacity(L): 600
Power(kW): 32
Recovery(%): 95
View More
8. Choosing the Right Supplier for Your Solvent Recovery Machine
As a leading manufacturer and exporter of solvent recovery machines, we understand the importance of reliability and performance. Here’s why businesses trust us:
20+ Years of Expertise: We design machines for durability and ease of use.
Custom Solutions: Tailor systems to your industry, chemical type, and volume.
Global Support: Installation training, maintenance guides, and spare parts available.
Conclusion: Is a Solvent Recovery Machine Worth It?
The caustic recovery process is no longer a luxury—it’s a smart business decision. By recycling solvents and caustic chemicals, you save money, comply with regulations, and contribute to a cleaner planet.
Whether you’re a small workshop or a large factory, there’s a solvent recovery system that fits your needs. Ready to explore your options? [Contact us] today for a free consultation and discover how much you can save!